NOW WE'RE GOING TO GET RIGHT INTO THE TRUMP ADMINISTRATION
NEWS.
JUST BRIGHTENS EVERY DAY, DOESN'T IT?
TODAY SCOTT PRUITT, THE NEW HEAD OF THE ENVIRONMENTAL PROTECTION
AGENCY WENT AGAINST THE ENTIRE SCIENTIFIC COMMUNITY BY SAYING
THAT CARBON DIOXIDE IS NOT A PRIMARY CONTRIBUTOR TO IMLOBBAL
WARM-- GLOBAL WARNING.
I WILL GO OUT ON A LIMB HERE AND SAY THAT THIS GUY MAY NOT BE THE
BEST CHOICE TO HEAD UP THE EPA, YES, BECAUSE --
(APPLAUSE) NOT ONLY, NOT ALL CAN HE NOT SEE
THE FOREST THROUGH THE TREES, HE WANTS TO CUT DOWN ALL THE TREES
AND BUILDS A CINNABON.
FOUR NEW JOBS, GUYS, FOUR NEW JOBS.
AFTER PRUITT'S STATEMENT ENVIRONMENTAL GROUPS ACTUALLY
AGREED THAT CARBON DIOXIDE ISN'T THE LEADING CREATOR OF
GREENHOUSE GASES ANY MORE.
IT'S ALL THE BULL [BLEEP] COMING OUT OF SCOTT PRUITT'S MOUTH.
THAT'S THE THING, BULL [BLEEP] IN OTHER RECENT ANNOINT
APPOINTMENT NEWS DONALD TRUMP ELECTED HIS AMBASSADOR TO RUSSIA
AND ITS FORMER UTAH GOV MER JON HUNTSMAN, PLEASE CONTROL YOUR
APPLAUSE.
(LAUGHTER) THIS IS GREAT NEWS FOR TRUMP.
HE FAINLLY HAS SOMEONE IN HIS ADMINISTRATION WHO IS ACTUALLY
SUPPOSED TO MEET WITH THE RUSSIANS.
(LAUGHTER) JON HUNTSMAN FIRST JOB AS
AMBASSADOR TO BE TO EXCHANGE GIFTS WITH HIS RUSSIAN
COUNTERPART AND THAT'S TOUGH.
BECAUSE WHAT DO YOU GIVE SOMEBODY WHO ALREADY GAVE YOU
THE WHITE HOUSE?
YOU CAN'T JUST HAND OVER AN EDIBLE ARRANGEMENT, DO YOU KNOW
WHAT I MEAN.
THE PEOPLE ARE REALLY EXCITED ABOUT THIS APPOINTMENT.
THERE IS EVEN GOING TO BE A MOVIE ABOUT JON HUNTSMAN JOINING
THE TRUMP ADMINISTRATION.
IT'S CALLED SO WHITE AND THE HUNTSMAN, COMING SOON TO AN IMAX
NEAR YOU.
(APPLAUSE) IN OTHER NEWS, WE THOUGHT THIS
STORY IS FUN.
DID YOU SEE THIS, IKEA JUST ANNOUNCED A NEW FURNITURE LINE
THAT IS SUPPOSED TO BE EASIER TO ASSEMBLE THAN TRADITIONAL IKEA
PRODUCTS.
THIS NEW LINE REQUIRES NO TOOLS, BECAUSE IT SNAPS TOGETHER IN
MINUTES.
NOW USUALLY THE ONLY THING THAT SNAPS WHILE MAKING EYE HE CANA
FURNITURE IS ME TRYING TO BUILD IKEA FURNITURE, WHERE IS SLOT B!
BUT WHEN ARE YOU DESIGNING YOUR HOME, THIS SNAP TOGETHER
FURNITURE IS THE PERFECT WAY TO SAY BOTH I'M CHEAP AND NOT GOOD
WITH TOOLS.
(LAUGHTER) A REAL WIN-WIN.
BUT YOU DON'T NEED TOOLS ANY MORE BUT DON'T WORRY IN KEEPING
WITH THE TRADITIONAL EYE HE CANA EXPERIENCE THEY'RE GOING TO
INCLUDE A BUNCH OF EXTRA SCREWS YOU CAN WONDER ABOUT.
LIKE WAIT, IS THIS THE JORGEN SHLORGEN OR THE GLOCKEN
SCHTUBEEN, I DON'T KNOW.
FINALLY WE HAD TO TELL YOU ABOUT A NEW SMARTPHONE APP THAT IS
GETTING A LOT OF PRESS RIGHT NOW.
THE APP WHICH IS CALLED O-CAST ALLOWS USERS, THIS IS TRUE, IT
ALLOWS USERS TO LICK THEIR PHONES SIMULATING ORAL PLEASURE
THAT CAN THEN BE SENT VIA BLUETOOTH TO A PARTNER'S SEX
TOY.
I KNOW.
I KNOW.
AND YOU THOUGHT ITS WITH ANNOYING WHEN PEOPLE FACETIMED
IN PUBLIC.
BUT THIS IS GREAT FOR PEOPLE WHO ARE IN LONG DISTANCE
RELATIONSHIPS AND AS AN ADDED BONUS, IT CLEANS ALL THOSE
FINGER SMUJS OFF YOUR PHONE SCREEN.
BUT APPARENTLY PEOPLE REALLY USE THIS TO HAVE SEX.
AND IT'S EXACTLY AS WOULD YOU EXPECT.
MOST GUYS CAN'T FIND THE HOME BUTTON.
BUT I FEEL LIKE-- DID YOU JUST WHOOP, IS THAT YOUR HUSBAND?
BOYFRIEND?
BOYFRIEND?
SHE WENT WHOOP.
HE WENT-- (LAUGHTER)
IT'S ALL RIGHT.
(APPLAUSE) THE IDEA IS YOU SAW THAT THEY
JUST HAD A KISS.
IT WAS VERY MUCH TWO DIFFERENT ATTITUDES HAVING A KISS.
IT WAS ONE PERSON GOING I STILL LOVE YOU.
AN HIM GOING HMMMM, WE'RE GOING IT TALK ABOUT THIS LATER.
CAN YOU IMAGINE, YOU HAVE TO LICK, YOU HAVE TO LICK THE
PHONE.
AND IF YOU'RE NOT GOOD AT IT, THE PHONE THEN GOES THAT'S OKAY,
HONESTLY.
APP THEN LATER YOU HEAR IT VIBRATING BY ITSELF.
SHOULD WE HAVE A LOOK AND SEE WHO OUR GUESTS ARE ON THE SLOW
TONIGHT?
IN THE BLUE ROOM, HE'S AN EMMY WINNING LEGEND YOU KNOW FROM
ROSANNE, THE BIG LEBOWSKI, TEN CLOVERFIELD LANE AND SO SO MUCH
MORE.
WE ARE SO THRILLED HE IS HERE.
ONE OF THE BEST ACTORS ON THE PLANET PLRKS JOHN GOODMAN IS
HERE TONIGHT.
(CHEERS AND APPLAUSE).
>> James: THERE HE IS.
JOHN, WERE YOU JUST TRYING YOUR PHONE?
IS THAT WHAT IT WAS.
>> I HAD TO CLEAN IT UP A LITTLE BIT.
>> James: REALLY.
>> I WAS RELAXING BEFORE THE SHOW.
>> James: YOU WERE RELAXING BEFORE THE SHOW.
ARE YOU AWAY FROM YOUR WIFE, MAKES SENSE.
>> THANK YOU.
>> James: GET BACK TO IT.
>> THANK YOU.
>> James: JOHN GOODMAN, EVERYBODY.
For more infomation >> Long Distance Oral Sex Is Here - Duration: 5:42.-------------------------------------------
John Goodman's New Star on the Hollywood Walk of Fame - Duration: 1:20.
WE HAVE TO CONGRATULATE YOU, JOHN, BECAUSE TOMORROW YOU'RE
GETTING YOUR STAR ON THE HOLLYWOOD WALK OF FAME.
(CHEERS AND APPLAUSE) >> WHAT?
WHAT?
>> YEAH.
>> James: YES, YOU ARE.
AND DO YOU KNOW WHO YOU'RE GOING TO BE NEXT TO?
>> A PIECE OF GUM.
>> James: YES.
>> AND DOG WASTE.
>> James: AN DOG WASTE.
>> NO, I DON'T KNOW.
>> James: WHO WOULD YOU LIKE TO BE NEXT TO?
>> OH, GEE, I DON'T KNOW, ANY OLD MOVIE STAR.
>> James: YEAH?
>> YEAH.
>> James: DO YOU KNOW WHEREABOUTS.
>> I'M JUST HAPPY TO BE THERE.
>> >> Senor.
>> James: YOU'RE RIGHT, IT'S INCREDIBLE.
>> YEAH, IT'S AN HONOR.
I'M VERY GRATEFUL FOR IT.
>> James: YOU SHOULD BE.
>> IT'S NOT THAT BIG A DEAL, HAVE I TWO.
>> James: SURE YOU DO.
WHO ARE YOU NEXT TO, ADAM.
>> WHICH STAR, BECAUSE MY FIRST STAR IS NEXT TO THE ECK WHICH
OX.
>> James: RIGHT-- AND THEN MY OTHER STAR IS IN FRONT OF THE
CHIPOTLE.
I THINK THAT ONE IS BETTER.
>> James: THAT ONE IS BETTER.
>> WHICH PART OF THE EQU, NOX?
>> THE BACK PART, WHERE THEY DO THE PILATES.
>> James: BECAUSE THAT IS SUCH A PART OF YOUR LIFE
>> I'VE THROWN UP THERE.
-------------------------------------------
Spoon: I Ain't The One - Duration: 4:11.
♪ ♪ ♪ ♪ ♪ ♪
♪ ♪ ♪ ♪ ♪ ♪
♪ ♪ ♪ ♪ WHEN THE MORNING'S RISING
AND LOOKING ON ME ♪ WHEN THE NIGHT COMES
KNOCKING AND KNOCKING ON ME ♪ I SAY
I AIN'T THE ONE ♪ I SAY
I AIN'T THE ONE ♪ I AIN'T THE ONE
THAT YOUR LOOKING FOR NOW ♪ WHEN THE MAN
COMES ASKING ♪ AND LOOKING FOR ME
WHEN THE LAW COMES KNOCKIN ♪ KNOCKIN ON ME
I AIN'T THE ONE NO, I AIN'T THE ONE
♪ I AIN'T THE ONE THAT YOUR LOOKING FOR NOW
♪ YEAH, I AIN'T THE ONE OH, I AIN'T THE ONE
♪ SO NOW I'M LEAVING YOU ALL BEHIND ME
♪ ♪ ♪ ♪ ♪ ♪
♪ ♪ ♪ ♪ ♪ ♪
♪ WHEN THE WORLD COMES CRASHING AND CRUMBLING
♪ ON ME WHEN THE NIGHT COMES KNOCKING
♪ AND KNOCKING ON ME I SAY
♪ I AIN'T THE ONE I AIN'T THE ONE
♪ HEY UH
♪ HEY UH
♪ I AIN'T THE ONE I AIN'T THE ONE
♪ SO NOW I'M LEAVING YOU ALL BEHIND ME ♪
♪ ♪ ♪ OH
♪ ♪ ♪ ♪ ♪ ♪
OH ♪ ♪ ♪
♪ ♪ ♪ ( CHEERS AND APPLAUSE )
-------------------------------------------
Adam Pally Got Fired By Ellen Burstyn - Duration: 2:32.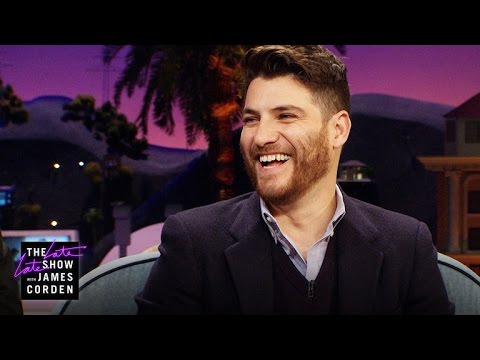
WHERE DID YOU WATCH THE SHOW.
>> WITH MY DAD, HE'S SUPER INTO MY CAREER AND CELEBRITY, KIND OF
LIKE A SHOW DAD.
>> James: RIGHT.
>> AND SO I NEVER IMAGINED YOU HIVING A SHOW DAD.
>> OH YEAH.
>> James: I IMAGINED YOUR DAD DISAPPROVED OF IT ALL.
>> I AM GOING TO TAKE THAT AS A COMPLIMENT AND, PIE DAD IS SUPER
INVESTED LIKE IN BETWEEN TAKES HE COMBS MY HAIR LIKE A HORSE.
>> SO A COUPLE WEEKS AGO, HE HAS THESE LIKE FAMOUS ACTRESSES THAT
HE CALLS HIS DIVAS.
>> James: RIGHT.
>> THAT HE FOLLOWS THEIR CAREERS, LIKE MERYL STREEP AND
THE GOOD WIFE, JULIANNA MAR GOLLIES.
AND ONE OF HIS DIVAS IS A FAMOUS ACTRESS ELLEN BU RSTYN WHO IS
AMAZING.
>> James: OF COURSE.
>> LUCKILY ENOUGH SHE HAD CAST ME IN A MOVE WREE SHE WAS GOING
TO DIRECT.
AND SO I WAS SO EXCITED IT WAS AN HONOR.
SO WE WERE DRIVING IN MY CAR AND THE PHONE RINGS AND YOU CAN SEE
ON THE THING TRK SAYS ELLEN BURNSTY, AM, OH MY GOD, YOU HAVE
TO-- MY DAD GETS STEFAN FROM-- LIKE OH MY GOD, YOU HAVE
TO PICK IT UP.
SO I WAS LIKE OKAY, OKAY, BUT DON'T SAY ANYTHING.
SO I PICK IT UP, AND SHE IS LIKE, ADAM, I AM SO GLAD I
CAUGHT YOU.
THIS IS SUCH A DIFFICULT PHONE CALL TO MAKE.
BUT-- BUT THE MOVIE IS HAVING TROUBLE GETTING FUNDING WITH AN
ACTOR OF YOUR CALIBER IN THE LEAD.
SO THE STUDIO, AND I HAVE COME TO THE DECISION THAT WE'RE GOING
TO LET YOU GO.
AND WE'RE GOING TO YOU KNOW, LOOK FOR SOMEONE WHO HAS A
LITTLE MORE STAR POWER.
AND I WAS LIKE OH, ELLEN, THANK YOU FOR CALLING ME AND TELLING
ME THAT.
I UNDERSTAND HOW THE WAY THE BUSINESS WORKS AND STUFF.
AND IT WAS AN HONOR TO WORK WITH YOU A LITTLE BIT.
AND SHE IS LIKE, THIS HAPPENS.
SHE'S GIVING ME A PEP TALK.
THIS HAPPENS, YOU KNOW, AND I'M SO SORRY.
SHE HANGS UP.
AND MY DAD TURNS TO ME AND HE GOES OH MY GOD, SHE SOUNDS
AMAZING.
(LAUGHTER).
>> James: OH MY GOSH.
>> I'M LIKE DAD, SHE IS AMAZING.
SHE JUST [BLEEP] FIRED ME.
-------------------------------------------
A Teenage Ai Fukuhara | Before They Were Superstars - Duration: 4:55.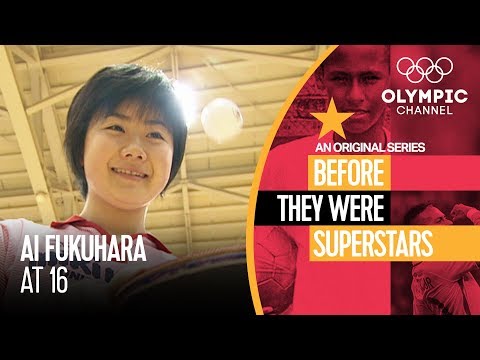
(BEFORE THEY WERE SUPERSTARS)
(AI FUKUHARA, AGE: 16 DATE: FEBRUARY 2005)
(SPORT: TABLE TENNIS LOCATION: AOMORI, JAPAN)
Situated at the northern tip of Honshu,
the biggest of Japan's four main islands,
is the city of Aomori.
Back in 2005, a 16-year-old Ai was living and training here.
Ai began playing table tennis at the age of three.
Too small to see over the table,
she would stand on upturned rubbish bins
and hit against older players.
Ai made rapid progress in the sport
and when she was 11,
she became the youngest player ever to be included
in the Japanese national team.
At 16, and ranked 23rd in the world,
she was even being hailed as
"The Tiger Woods of table tennis".
I'm no such thing.
Tiger Woods has achieved such a lot,
and there's been so much written about him.
He's a great person, and I feel sorry for him
if they compare me to him!
I have been playing ever since I was a little girl.
I don't spend too much time thinking about why I play,
I just do.
In 2003, Ai made her breakthrough on the world stage
when she reached the quarterfinals of
the World Championships,
before losing out to the then world number one,
Zhang Yining of China.
I was fortunate to progress to the last eight.
Next time, I don't know how far I can go.
I want to play like it's my first time again.
Ai practised for six hours each day
after going to school in the morning.
Her training sessions were supervised
by two female Chinese coaches.
Her dad, Takehiko, was never far away either,
offering his own advice.
At 16, Ai was already fluent in Mandarin,
and was planning to move from Japan to China
to play in the Chinese Super League.
It was hoped that the move
would help her development as a player.
The playing conditions in the Chinese League are different.
There's a lively atmosphere, and it's noisy.
It's going to be difficult for me to adjust.
I hope I become a more consistent
and competitive player.
Chinese players have great skill,
and are the best in the world.
There are some pretty decent European players out there too,
but the top of the rankings is filled with
players from China.
It will be a great experience for her to be playing
amongst them.
At this stage of her career,
Ai was attracting a growing army of fans.
She had been voted by Japanese children
as their favourite sportswoman.
It's great that I have many fans,
but I don't like to be the centre of attention.
Sometimes I run away from people.
Ai has gone on to become
one of the most recognisable faces in Japan,
and is also hugely popular in China.
-------------------------------------------
The Internet Warriors - Duration: 21:28.
-------------------------------------------
How To Make St Patricks Day Rainbow Skittles Rice Krispies Cupcake Dessert DIY Kids Cooking Crafts - Duration: 15:39.
Top of the morning to ya! I'm Chef Ava...
And today I'll be your guide on how to make St Patricks Day Rice Krispies rainbow skittles cupcake dessert.
Using edible gold spray paint.
The other items you'll need to make this delicious dessert will be marshmallows, rice krispies, gold coins candy, some white frosting,
vanilla cupcakes and rainbow skittles.
I have my lucky assistant here.
hello!
He's my very own leprechaun.
Let's get started.
Alright leprechaun put the mallows in.
We have our five tablespoons of butter, and our six cups of mini marshmallows and now we are going to add ten cups of rice krispies.
That's a lot of rice krispies.
Now we got to pack it in.
Help me leprechaun!
There we go. While this is cooling off we will be frosting our cupcakes!
Last one.
There we go.
Now comes the coolest part.
You'll want to put the cupcakes on top of paper so that when you spray the cupcakes it won't get on the counter.
We will be using this gold color mist made by Wilton.
It's like edible spray paint and I love to spray paint.
This is our first try in history.
It smells like real spray paint.
Now time to top on these gold chocolate coins.
Check out that bling.
So we cut our rice krispies in half so we're going to make a rainbow arch.
Oh I'm so strong.
So what you want to do is you want to kind of bend both sides so it makes like a little arch.
ou just want to stick them side by side.
Alright how does it look? Does it look like a rainbow?
Now we just have to frost it and put our rainbow skittles on.
So you got our cake frosted and now all we have to add are our rainbow skittles.
Red, orange, yellow, green, purple!
That's going to be our pattern.
There we go. It's done!
We want some fluffy blue clouds at the end of our rainbow so let's spray paint some more cupcakes.
Now let's stick it all together.
Let's get our gold coins in the middle and our fluffy blue clouds at the end.
There we go.
I want a little taste.
Yum magically delicious.
What the...you have blue hair!
Whoa your hair looks awesome. Same with yours, it's so blue.
Weeee!
Oh he's such a cute little leprechaun.
Thank you so much for making this St Patricks Day rainbow dessert with me.
Leprechaun out.
Let's dance our Irish jigg.
Don't forget to like, subscribe and comment below on what your favorite color is.
Or what would you buy if you found a pot of gold?
I would by a golden beard.
Money.
Don't be touching my gold.
-------------------------------------------
Tutorial de magia: Globo Atravesado - magic tutorial: balloon penetration - Duration: 3:44.
the best book of magic
the balloon crossed
Magic trick
tutorial
The effect:
Today I'm going to do a magic trick with a balloon
We introduce the balloon into a plastic tube
the balloon goes a fair bit
We go through everything with a sharp pencil
draw pencil
the balloon has not exploited
the balloon is intact
the tube is not souped
You can give all to examine
tutorial:
I will use a transparent tube for explanation
the balloon is not souped
We wring the globe as if we did Balloon Modelling
We hide narrowing hand
thus, the appearance of the balloon is normal
We introduce the balloon into the cylinder
without narrowing see
prepared control part
looking through the holes
Carefully introduce the pencil
We show the result
and rid the rotation of the globe
remove the pencil
extract the globe
and give all to examine
Congratulations, you came to the end
-------------------------------------------
ALLAHU AKBAR..!! 5 Benda dari Surga ini Ada di Bumi bahkan ada yang di INDONESIA - Duration: 6:38.
-------------------------------------------
ПОКУПКИ ОДЕЖДЫ с ПРИМЕРКОЙ с Aliexpress! Сумки #174 - Duration: 8:59.
-------------------------------------------
Eli Sarayli Gel Ayrilmayaq 2017 YENI !!!! - Duration: 3:41.
-------------------------------------------
I tried a burger for the first time l Losing my burger virginity l 난생 처음으로 햄버거를 먹어 봤다. - Duration: 6:40.
Hey, guys! Welcome to my channel!
So, I decided to start a new series on my channel
called "First Time", where I basically venture out of my comfort zone,
and try new things while also sharing my experience with you guys!
I thought it would be fitting for me to start off this series with me trying a burger for the first time.
Now, I know what you're thinking.
"How has she never tried a burger before? Like, are you serious?"
And yeah, same.
No one believes me when I say that I've never tried a burger because
I've lived most of my life in America, I've grown up in America,
and it's really absurd that I've never been tempted to actually try a burger.
So, let me just take some time to give you guys an explanation as to why I've never tried a burger.
No, I'm not a vegetarian, but meat isn't my favorite thing to eat.
And I feel like the main reason why I've never tried a burger
is that I don't eat outside.
Going out and eating something at a restaurant is just for fancy occasions
like birthdays. And even on my birthday, I would just be too lazy to go out and eat,
so we'd just order pizza, or something like that.
Because I haven't really been exposed to fast food restaurants
and I have never felt the need to go outside and find something to eat,
I feel like that's the main reason why I've never tried a burger.
I just don't eat outside.
And also, another reason is, I'm not really adventurous with my food.
If I had to choose between something that I'm 100% sure I'll like
versus something that I'm not really sure I'll like,
I'll definitely go for the one that I know I'll like.
So, for example, if I go to a fast food restaurant,
when I do, which is very rare, maybe when I'm hanging out with my friends,
I would just order chicken nuggets or french fries
as opposed to a burger.
It's not that I don't try new things.
I do try new food, obviously.
But, if it doesn't look appetizing, I won't try it.
And burgers are one of those things,
when I look at them, they don't really look appetizing
I don't drool over a picture of a burger.
I'm just weird.
A burger is just one of the many foods that I haven't tried before.
And again, it makes sense because I rarely eat outside.
My mom likes to cook, and I like to eat her food sooo
Last Saturday, my friend Elena and I went to In-n-Out,
and I ate a burger for the first time.
I'm not sure what burger it was, but it was #3.
It's the one with no cheese in it, I believe.
I don't know what it's called, and I had grilled onions in it.
And I also got a strawberry milkshake and fries.
And I ended up eating the whole burger, but
I couldn't finish the milkshake and the fries because I was too full after the burger.
The following clips are my reacion to eating a burger for the first time.
She finished.
Uh, I feel like throwing up!
She's actually going to be sick, and I'm about to make her walk everywhere
to work this off.
Ah, food coma.
So, those were all the clips.
I couldn't film more because my camera didn't have enough batteries,
and it kept shutting down after 30 seconds of filming,
so that was all the footage that I got.
Bottom line, it was good.
I like it, it's good.
But I can live without it.
I feel like it's not something I would crave.
But you know, you never know. Maybe because I've only tried it once.
So my first impression was overall positive.
The taste wasn't what I was expecting, but it was good.
It was like a good surprise, you know?
I snapchatted my sister after I tried a burger,
and she asked me how it went.
and I told her exactly what I told you guys about how I could live without it,
and she just sent me a big fat F.
So yeah, clearly we have different tastes.
But, it's okay.
Leave a comment down below on what you want me to try next.
I could be food or it could be anything in general, like skiing
or something like that.
You name it, I probably haven't done it.
And if you enjoyed, make sure to give it a thumbs up.
I would really appreciate it.
And yeah, I'll see you guys in my next video. Bye!
-------------------------------------------
Free Hash Power !! Free BITCOIN Cloud Mining Gifts !!! Up to 1000 Gh Free - Duration: 7:00.
-------------------------------------------
Wat Mahathat, Old Ayutthaya : ENTRY FEE (for you = 50 Baht, for me = Free) - Duration: 18:15.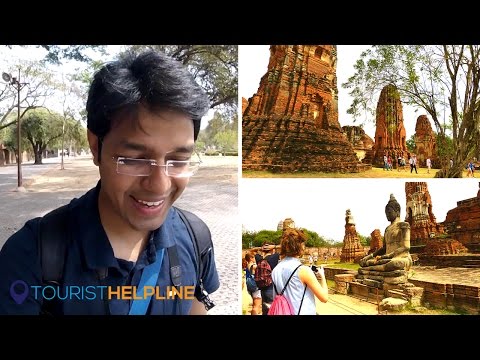
It is 10 am and I've just checked out of the hotel
I am going to visit Old Ayutthaya
which was capital of ancient Thailand
There are temples and ruins of the old city
People have kept their vehicle's headlights on even during the day time
It may be because of the traffic rule or due the awareness among the people
especially 2 wheelers should always have their headlights on
This is Ayutthaya City Municipality's office
I can see people use tinted car glasses in Thailand
It is not allowed in India
These mini-vans are going to Bankok
You can see these vans all over Thailand
Last year, I used a similar van on Cambodia's trip
The wide traffic-less roads and luxurious cars sometimes makes me feel that I am somewhere in Europe
The sign boards written in Thai are the only things which makes me realise that this is Thailand
I am impressed by the infrastructural development
I stopped to see a message which I have got from a Couchsurfer based in Ayutthaya
Yesterday I sent couch requests to some of the hosts in this city
He is one of them
He may be calling me in sometime
I was talking to the couchsurfing guy
He said, that being a Monday he has to be in office. So he won't be able to come & show me this place
But he gave me a much-required advice of all the things to do and worth visiting places in Ayutthaya
after visiting the place, today I am going to Hitchhike
A direction board to Wat Mahathat
Wat means a temple. For eg. Angkor wat
Now I am going towards Wat Mahathat
Those are the ruins of the ancient capital
You can explore this place on a bike
Rent a bike for a day in just 40 Baht
Entry is free as Thailand is currently in a period of national mourning after the passing of the King
This temple complex reminds me of Cambodia's Angkor Wat
This is UNESCO World Heritage site
This temple is tilting to one side
These all were built in 14th century
So these building are almost 400 years old
Lots of people visit this place to see this..
The stone Buddha head entwined in tree roots
Its a bright sunny day, though not hot
I can feel the cool breeze
This is another worth visiting place
This structure must be an important part of some building in ancient time
Do keep lot of water and something to eat whenever you visit this place
because you may loose a lot of energy and fluids while walking in this huge complex
Keep munching to maintain your energy level
This place is so tranquill
that is why it attracts lot of visitors
Please respect the rules of this place
Touching and climbing on the statues and other vital structures is strictly prohibited
Let me share this..
I have seen a lot of tourists from different parts of the world since morning
but didn't see any Indian till now
Also.. I saw many solo female travellers
whereas in India, there are lot of apprehensions of travelling solo, especially when it comes to girls
Friends..
Situation is different in other parts of the world
You have to step out of your home to experience a different world
Many girls from other countries travel independently, travel solo
Even girls from our neighbour country like China are exploring countries alone.
You just have to be careful & remember few basic things and you'll be ready to venture out
Being careful doesn't mean that you have to restrict yourself from talking with strangers ...
it doesn't mean that you don't have to mingle with others..
It means - talk to strangers, make new friends, every moment try something new
It makes you so confident that you can tackle odd situations single handedly
You may commit mistakes
By making mistakes you will in fact learn valuable life lessons
Making mistakes is the key to making progress
why do i get tired very soon!
is it because I am carrying a lot of weight!
I could have left my bags at the hotel, but...
I didn't want to go back to collect my bags after visiting this place
I am planning to directly go to the highway to hitchhike
Though I am tired, yet I am enjoying
The cool breeze, this water body, the whole environment..
I'll stay here until I want
Where I want to go!
I don't know
This place is called 'Vihar'
This structure used to be the part of a building
in between are the pillars
and the elevated structure.. there.. used to be a platform to keep Buddha idol
The names like Vihar... Ayutthaya...
are very similar to Hindi, Sanskrit and Pali
I read somewhere that many words in Thai language are borrowed from Sanskrit and Pali
Actually, Thailand seem like a mix of Indo-Chinese cultural influences
Many words of the modern Thai language have been derived from Chinese
Thailand has drawn great inspiration from India be it literature, theatre, arts, language, astrology, etc.
I was looking at the map of Ancient Thailand
It was known as Siam in those days
If I am not wrong.... Laos and Cambodia were also the part of Siam in 12th or 13th century
But eventually due to attacks from the Myanmar they lost their territory
Due to the conflicts with other kingdoms...
Cambodia, Laos and others got separated from the erstwhile Siam
and today, Cambodia, Laos, Vietnam and Thailand have their Independent existence
This place - Ayutthaya used to be the capital of ancient Thailand
and eventually, after many centuries Bangkok became the capital of the modern Thailand
You can spot such Tourist Information kiosks at prominent tourist places
I met him in the morning at the entry gate
A tourist can dial 1155 from anywhere in Thailand to get police assistance
This number is also toll free
These structures seem to be quite different
It is said that these are the royal temples of the royal palace
These temples are different from all other structures here
A support has been provided to the old wall which was tilting on one side
Since morning I haven't seen any toilet or a drinking water place
whereas, there were many good toilets built around Angkor wat temple complex
I did a full day trip on tuk-tuk at Angkor Wat
Though the entry ticket was very expensive - 20 US Dollars
But they provided a very neat and clean toilet near every temple in these 20 USD
Its different here
Although there is no place of drinking water even in Angkor wat and even here
Please keep a bottle of water with you
Suddenly, I heard chants of mantras
Going to see whats happening !
Who are the people chanting these! What is the occasion !!
The mantras were being chanted at this place
Isn't their way of worshipping very close to ours!
Elements like Fire, incense sticks, etc. are common in India and Thailand
quite expensive !!
photograph please!
Now, I am on the road... Lets start 'Mission Hitch-Hiking' !!
-------------------------------------------
Most Amazing Wild Animals Attacks | learn wild animals names Animal Sounds funny animals compilation - Duration: 1:32:06.
Most Amazing Wild Animals Attacks learn wild animals names Animal Sounds funny animals compilation nursery rhymes for children
-------------------------------------------
Мастер-класс - Колье "МЕДУЗА" ✿ DIY - Necklace "JELLYFISH" ✿ ENG SUB - Duration: 18:16.
Hello! I'm Karina Formanova. Welcome to Evrazhka Studio.
In this video I continue to work with my texture sheets and want to show you a mix of two techniques
— Sutton Slice and «gel filling».
I wanted to show it to you for a long time, and finally I'm holding appropriate textures.
I have told you about them, how to use them, and how to treat it in a previous video.
The link is below. You should take a look if you haven't seen it.
This time we will work with the texture #3, but #1 and #2 are perfect too.
In fact, you can use any texture with a not very dense pattern.
«G. F. Art Tools» manufactures all five textures by my original drawings.
Also they still have a lot of cool texture sheets by drawings of artist Irina Tokmakova.
Not to speak of awesome cutters!
Highly recommend a look to visit them. All links are in the description below.
Let's, get to work. Full list of all necessary materials and tools is in the description below.
As I said, we need a texture with a not very dense pattern for this technique.
If convex elements are located too close to each other, then this effect will be gone.
Also it is very important for clay to easily separate from the texture later on.
Therefore, I suggest to take a silicone spray as a separator in this case.
Spray it on the texture and blot it with a napkin.
Choose a place with the most appropriate pattern.
Knead dark brown clay and make a layer.
Press it into the texture. Add more pieces if necessary.
Then cut upper layers with a thin sharp blade.
Don't hurry and make it gradually, in thin slices.
Otherwise there is a great risk to accidentally damage the texture.
We need to cut clay so that it remains only in recesses.
It should not stay on convex parts.
Accuracy of the entire work will depend on it.
If small items fall out, then just re-fill this place with a small piece of clay and cut the excess.
Postpone the texture for now and roll out a clay layer with a thickness of about 1.5 mm.
Cut out the shape with a cutter.
Put a metal leaf piece.
Make cracks.
You can stretch the layer with your hands, or can roll it through a pasta machine. I stretch it in my hands.
Then put it on a tile which you will bake.
Put it smoothly, without air bubbles.
Now we take our texture and put it on the layer with the metal leaf.
Roll it with a roller make clay from the texture bond well to the metal leaf.
As I said before, at this stage it is very important for clay to easily unstick from the texture sheet.
It is not critical for classic Sutton Slice, because clay adheres well to clay.
But clay attaches to a metal leaf not so willingly.
But all separate very easily thanks to use of silicon spray.
Now cut out the desired shape with a cutter. Remove excess clay and clean up the edge with a knife.
Now cut out the desired shape with a cutter. Remove excess clay and clean up the edge with a knife.
Its length should be slightly larger than the circumference of the oval, and its thickness should be about 2-3 mm.
Cut out a thin strip with a ruler.
Wrap it around the main element.
The rim should fit snugly to the detail and to the tile, with no gaps.
Cut a strip joint to joint.
Smooth the seam gently with a silicone spatula.
Bake it for 15 minutes.
After cooling, color cells with a colored liquid clay.
You can see what and how to stain liquid clay in my separate video.
The link is in the description below.
Those who follow my tutorials are already familiar with this process.
I often use colored liquid clay in the work.
One color is enough for small cells, and it is possible to make smooth transitions in large cells.
Slightly mix colors together to make boundaries of colors smooth.
Small dots and stripes can easily be removed from the metal leaf, so be especially careful painting over these places.
I missed the small cell during filling, but noticed it only in the final.
Although the work is not spoiled.
Now bake the item for 15 minutes.
While it is baking, prepare wire elements.
You can take it from ordinary cable.
We need quite thick copper wire for this work.
I have a diameter of 1.5 mm.
I don't advise to take a wire thinner than 1 mm. It will not have sufficient rigidity.
Cut it into pieces of length 7 — 10 cm. We need at least 4 pieces.
Align them slightly and bend them in the middle at right angles.
We need a gas burner to form the balls.
If you don't have it, the same can be done on a gas stove.
Or even skip this step. Later I will tell you what items you can make instead of it.
And please do not forget about safety.
Open flame of burner it is not a miserable 110 degrees in the oven. Please be careful!
And so, take the wire with tweezers and hold the tip at the end of the flame,
and heat it until copper begins to melt and there will be a ball.
It is important to capture the moment when the ball has become round, but not too large.
Toss the wire into water, so it cools faster. Make balls on both sides.
Wire have black soot after annealing.
We need water and usual citric acid to remove it.
Pour some acid and put wires.
Leave it for some time to soot came down. I usually leave it for the night.
Copper have become pure pink.
Divide the wire in half.
Make a few bends with the pliers.
Wire became soft and easily bent after annealing.
In order to give stiffness to wire and to make element more interesting, beat wire with a flat side of a hammer.
I have a small bench block.
You can also use an anvil or, for example, the flat side of another hammer.
You can use any stiff flat metal surface.
Beat slowly and carefully across the surface of the bent portion.
Do not touch the straight end yet.
Repeat with all items.
If you are not able to make balls, you can just bite off a wire with a desired length
and make a neat tip with a needle file.
Bend the wire in several places, leaving the end free.
And just beat it with a hammer, carefully beating the wire end.
It will become more wide and flat.
Such elements also will look very good in our jewelry.
Now we need to put all elements in a correct order.
For convenience, I have circled the pendant outline on a paper sheet and use it as a guidance.
At this stage the most important thing is to consider length of each element.
Mark the desired length with a marker.
Take the central element and bite off excess wire, leaving about 1 cm from the mark.
Bend a loop with pliers.
Beat it with a hammer so it will become hard and flat.
Lubricate the loop with super glue and glue the item into its place.
Make the same with all elements.
Roll out a clay layer with a thickness of about 1.5 mm.
Grease the reverse side with liquid clay, including between the loops.
Close the side by the layer and put it on a sheet of paper.
Press it carefully that clay is well distributed between metal elements and the surface became smooth.
Cut clay along the contour.
Remove remaining liquid clay.
Cut the contour at an angle.
Smooth the surface with your fingers.
Apply texture in any convenient way.
You can use a toothbrush, a stiff brush, a sponge, or fine texture, like me.
I have a silicone mold from a wooden board.
Finalize it with a needle in places where the texture has not squeezed.
Put a personal stamp if you want.
In this pendant I will make a traditional mount.
Roll out a small layer of clay with a thickness of about 1.5 mm.
Cut off one side and wrap it around the rod with a diameter of 3-4 mm.
Smooth the joint.
Cut the desired length.
Apply a thin strip of liquid clay and put the mount into place.
Bake the pendant for 30 minutes.
Take out the rod after cooling.
If you want a pendant to be accurate and the resin lens form to be perfectly flat grind the sides.
Firstly I grind with sandpaper #600, then #800, #1000 and #1500.
Sand the mount with very fine sandpaper only.
You can grind metal elements with it too.
Rub ends and the mount with clean dry cloth to make them slightly shiny.
Mix epoxy resin.
The proportions for mixing and time for curing are in the instruction for your resin.
Follow it clearly.
Mix it thoroughly and leave the resin to obtain a required density.
For convenience, I cut a hole in a styrofoam piece for the mount.
So the pendant will lie perfectly straight.
Fill the lens.
If you wish, you can drop a resin drop on each end of wires.
You will get a very interesting effect.
Cover the pendant from dust and leave it to fully cure.
We need a memory wire for assembling the pendant, slightly more than one loop.
And hollow rubber cord.
Thread the wire in the cord.
Put on a black bead.
Bend 7 mm wire at a right angle with pliers.
Make a loop.
This wire is quite stiff, but with repeated flexion — extension may even break down.
So make it right the first time.
Now find the second wire end and cut excess cord.
Put on the pendant.
Thread a bead and bend another loop similarly.
Hang a clasp.
I made this hook and a ring of the same copper wire.
If you wonder how to make it, let me know in the comments below and I will make a separate tutorial.
Ends of the necklace are close to each other in a free state, and clasp unhooks easily.
However, clasp straightens when worn under the weight of the necklace and holds up very well.
Well, our necklace is ready.
Necklace is very stylish and quite large.
It is the perfect addition to an open neckline of your dress.
It glows in the sun beautifully, and small resin drops give an interesting effect.
In addition, they are very pleasant to the touch.
Perhaps the only thing that bothers me is the wire color at the necklace base.
It is silver, but everything else is copper color.
It's not a very efficient solution, but, unfortunately, I didn't have the basics of a different color.
I remind you that all my textures you can buy in G.F.Art Tools store.
Links are in the description below.
If you liked this tutorial, share it with your friends.
And subscribe to the channel — there is a lot more ahead.
And if you want to support the channel financially, you can become my patron.
You'll have access to new videos and my advice.
Details are in the description below.
You can buy my jewelry in Vkontakte group.
And I will say goodbye and wait for your comments.
Thank you all for watching and bye!
-------------------------------------------
State tax refunds will come within four to 16 weeks depending on filing date - Duration: 0:50.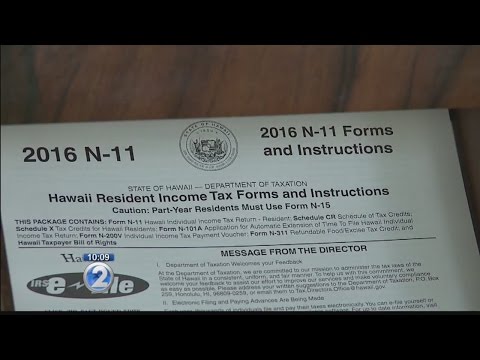
IF YOU'RE GETTING READY TO FILE
YOUR TAXES -- THE STATE SAYS THE
SOONER YOU FILE, THE BETTER IF
YOU'RE HOPING TO GET A QUICK
REFUND.
RIGHT NOW TAX REFUNDS ARE BEING
DELIVERED
REFUND COULD TAKE AS LONG AS 16
WEEKS.
THE STATE SAYS THE LATEST DATE
YOU CAN
EXPECT TO GET YOUR REFUND IS
JULY 20TH --
NICKI ANN THOMPSON /
THE STATE ALSO SAYS PAPERLESS
FILING IS THE
BEST WAY TO ENSURE YOU GET YOUR
RETURN BACK
IN THE FASTEST AMOUNT OF TIME
POSSIBLE.
-------------------------------------------
Oggy and the Cockroaches ★ NEW series 2017 cartoon for kids ► Special Collection 2016 Part 155 - Duration: 26:46.
Oggy and the Cockroaches ★ NEW series 2017 cartoon for kids ► Special Collection 2016 Part 155
Oggy and the Cockroaches ★ NEW series 2017 cartoon for kids ► Special Collection 2016 Part 155
Oggy and the Cockroaches ★ NEW series 2017 cartoon for kids ► Special Collection 2016 Part 155
-------------------------------------------
How To See Live Footage Of Whole World CCTV Camera On Your Android Phone | See LIVE CCTV In Mobile - Duration: 8:27.
Hit LIKE & SHARE :)
Thanks For Watching :))
-------------------------------------------
"Burning Man" Ft. Post Malone
-------------------------------------------
Trương Thơ với Thao Nguyen và 3 người khác. 21 tháng 10 2015 · - Duration: 0:53.
-------------------------------------------
Magische Musik der akustischen Gitarre, Frieden Musik, ruhige Musik und Ruhen, Schlafen - Duration: 30:46.
-------------------------------------------
nightmare || ڈراونے خواب بالکل نہیں آئیں گے اگر اآپ یہ پڑھ کر سوئیں گے - Duration: 1:02.
-------------------------------------------
【WiiU版】ゼルダの伝説-ブレス オブ ザ ワイルド-【実況】~Part2~ - Duration: 38:31.
-------------------------------------------
"Power Rangers" Movie
-------------------------------------------
For more infomation >> "Power Rangers" Movie-------------------------------------------
Citroën DS3 1.6 THP 200 Racing - Duration: 0:57.
-------------------------------------------
For more infomation >> Citroën DS3 1.6 THP 200 Racing - Duration: 0:57.-------------------------------------------
Citroën Grand C4 Picasso 1.6 THP Business - Duration: 1:02.
-------------------------------------------
For more infomation >> Citroën Grand C4 Picasso 1.6 THP Business - Duration: 1:02.-------------------------------------------
Citroën C3 1.2 VTi Collection Airco/Led dagrijverlichting - Duration: 0:59.
-------------------------------------------
For more infomation >> Citroën C3 1.2 VTi Collection Airco/Led dagrijverlichting - Duration: 0:59.-------------------------------------------
Citroën DS5 1.6 THP Sport Chic 200pk/Leder/Bi-Xenon - Duration: 1:01.
-------------------------------------------
For more infomation >> Citroën DS5 1.6 THP Sport Chic 200pk/Leder/Bi-Xenon - Duration: 1:01.-------------------------------------------
Citroën C4 Picasso 1.6 THP Business Airco/Achteruitrijcamera/Keyless Entry - Duration: 0:58.
-------------------------------------------
For more infomation >> Citroën C4 Picasso 1.6 THP Business Airco/Achteruitrijcamera/Keyless Entry - Duration: 0:58.-------------------------------------------
Citroën C4 Picasso 1.6 THP Ligne Bns Acc/Cruise Control/Navi - Duration: 1:02.
-------------------------------------------
For more infomation >> Citroën C4 Picasso 1.6 THP Ligne Bns Acc/Cruise Control/Navi - Duration: 1:02.-------------------------------------------
Citroën C3 Picasso 1.6 VTi Exclusief Airco/Cruise Control/Dakrails/Lmv - Duration: 0:59.
-------------------------------------------
For more infomation >> Citroën C3 Picasso 1.6 VTi Exclusief Airco/Cruise Control/Dakrails/Lmv - Duration: 0:59.-------------------------------------------
Citroën C1 1.0 Led COLLECTION * 40.902 Km * 5 Deurs * Airco * - Duration: 0:58.
-------------------------------------------
For more infomation >> Citroën C1 1.0 Led COLLECTION * 40.902 Km * 5 Deurs * Airco * - Duration: 0:58.-------------------------------------------
Citroën Grand C4 Picasso 1.2 PureT. Tendance autom. Airco/band.sp.contr.syst./regensensor - Duration: 1:02.
-------------------------------------------
For more infomation >> Citroën Grand C4 Picasso 1.2 PureT. Tendance autom. Airco/band.sp.contr.syst./regensensor - Duration: 1:02.-------------------------------------------
Citroën C4 Cactus 1.2 VTi Business Navi/Pdc/Achteruitrijcamera/Navi/Cruise control - Duration: 1:07.
-------------------------------------------
For more infomation >> Citroën C4 Cactus 1.2 VTi Business Navi/Pdc/Achteruitrijcamera/Navi/Cruise control - Duration: 1:07.-------------------------------------------
Citroën C3 Picasso 1.6 VTi Tendance Airco/elek. ramen voor/mistlampen voor - Duration: 1:00.
-------------------------------------------
For more infomation >> Citroën C3 Picasso 1.6 VTi Tendance Airco/elek. ramen voor/mistlampen voor - Duration: 1:00.-------------------------------------------
Citroën C4 Picasso 1.6 BlueHDi Automaat(al6)Intens. - Duration: 0:56.
-------------------------------------------
For more infomation >> Citroën C4 Picasso 1.6 BlueHDi Automaat(al6)Intens. - Duration: 0:56.-------------------------------------------
Citroën Berlingo 1.6 HDI 500 Club Ec. Buitenspiegels elek./Zijschuifdeur rechts - Duration: 1:06.
-------------------------------------------
For more infomation >> Citroën Berlingo 1.6 HDI 500 Club Ec. Buitenspiegels elek./Zijschuifdeur rechts - Duration: 1:06.-------------------------------------------
Citroën Grand C4 Picasso 1.6 THP Intensive Rondomzichtcamera/Autom. Airco/Keyless entry - Duration: 1:03.
-------------------------------------------
For more infomation >> Citroën Grand C4 Picasso 1.6 THP Intensive Rondomzichtcamera/Autom. Airco/Keyless entry - Duration: 1:03.-------------------------------------------
Citroën C1 1.2 E-VTI 82 PK 5DR Shine ABS/Airco/Lichtmetalen velgen - Duration: 1:05.
-------------------------------------------
For more infomation >> Citroën C1 1.2 E-VTI 82 PK 5DR Shine ABS/Airco/Lichtmetalen velgen - Duration: 1:05.-------------------------------------------
Citroën C3 1.2 VTI COLLECTION / ECC / PDC / DEALER ONDERH. !! - Duration: 0:54.
-------------------------------------------
For more infomation >> Citroën C3 1.2 VTI COLLECTION / ECC / PDC / DEALER ONDERH. !! - Duration: 0:54.-------------------------------------------
Citroën C1 5DRS AMBIANCE AUTOMAAT KEURIG - Duration: 0:54.
-------------------------------------------
For more infomation >> Citroën C1 5DRS AMBIANCE AUTOMAAT KEURIG - Duration: 0:54.-------------------------------------------
Citroën C4 Cactus 1.2 82PK SHINE * NAVI * LMV * CLIMA * PARK.H. * - Duration: 1:05.
-------------------------------------------
For more infomation >> Citroën C4 Cactus 1.2 82PK SHINE * NAVI * LMV * CLIMA * PARK.H. * - Duration: 1:05.-------------------------------------------
Citroën DS3 1.2 VTi 82pk CHIC * LEDER * CLIMA * VERWACHT * - Duration: 0:41.
-------------------------------------------
For more infomation >> Citroën DS3 1.2 VTi 82pk CHIC * LEDER * CLIMA * VERWACHT * - Duration: 0:41.-------------------------------------------
Amac TV - iHealth Core slimme weegschaal - Duration: 0:58.
-------------------------------------------
For more infomation >> Amac TV - iHealth Core slimme weegschaal - Duration: 0:58.-------------------------------------------
Get more Views and Subscrib...
-------------------------------------------
Mazda CX-5 2.0 SkyActiv-G 165 GT-M Line 2WD - Duration: 1:03.
-------------------------------------------
「絵画の歴史」対談その5「写真 真実 そして絵画」D・ホックニー×M・ゲイフォード - Duration: 1:59.
-------------------------------------------
Paw Patrol Pj Masks COLLECTION more 15 min for Kids Finger Family Nursery Rhymes Learning Video - Duration: 16:15.
Paw Patrol Pj Masks COLLECTION more 15 min for Kids Finger Family Nursery Rhymes Learning Video
-------------------------------------------
Culture Beat - World in your hands (Official video with lyrics) - Duration: 4:16.
You can walk on the water, shine like a diamond Ring the bells of fortune if you dare
You can make any move that you wanna make Take everything that you can if you dare
Just think the world is in your hands (x2)
Think the world is in your hands
Just think the world is in your hands
Stress on my mind, think I'll end it all, people tell me to stand tall
But I don't want to live, got nothing to give and I'm tired of hitting walls
They don't understand from where I come, my past not a pretty one
Scars, never stars, now I'm ready to quit and let this life be done
Some tell me to hold on, tell me to be strong, but the battle's too long
No fight left in me, but they don't comprehend that my will is all gone
Nothing to grasp, hope is past and my faith is in the trash
So save the love that you think I need, I'm going out with a blast... blast
You can walk on the water, shine like a diamond Ring the bells of fortune if you dare
You can make any move that you want to make Take everything that you can if you dare
Just think the world is in your hands (x2)
Think the world is in your hands
Just think the world is in your hands
Troubles got me down, never got a break, just pain and heartache
Not looking for a reason to go on, no more, I've had all I can take
I'm tired of the same old thing, same old scene, death must now be king
I give up, I don't want to live up to the wicked hopes of society
Some say excel, but I still fail so well, just call me a pro
Reasons for failing, truth be known, I really don't care to know
It's time to move on, time to be gone, farewell to my king
Just want to end this losing trend with a bullet and a shot of gin, a gin...
You can walk on the water, shine like a diamond Ring the bells of fortune if you dare
You can make any move that you want to make Take everything that you can if you dare
Just think the world is in your hands (x2)
Think the world is in your hands
Just think the world is in your hands (x3)
Think the world is in your hands
Just think the world is in your hands
-------------------------------------------
Alfa Romeo Stelvio 2017 || OFFICIAL PREMIERE (ENG. SUBS) - Duration: 5:05.
Hi guys, welcome back to my channel!
I went to the Alfa Romeo Stelvio official premiere held by Autozatti Parma and they revealed the brand new SUV of Alfa Romeo
in particular the Q4 four wheel drive that normally is rear wheel drive but in extreme conditions switch to four wheel drive.
It has the 2.0 liter turbocharged engine with 280hp.
Let's see the video of the premiere and the speech that one of the Alfa Romeo expert gave.
Stelvio in the first SUV of Alfa Romeo and for this reason tonight is a very unique one.
Lots of things distinguish this SUV from the others: firstly, it is an Alfa Romeo,
it has the driving position of a SUV (12 cm higher than the Giulia) but at the same time it has a sporty character.
Secondly, the internal ergonomics: it has a very enveloping driver seat with a stealing wheel similar to the F1 ones.
But above all it offers a direct and pure driving experience given from its steeling wheel, gear shifter and brakes.
As far as the internal design is concerned it is typical of Alfa Romeo.
It has a very low aerodynamics coefficient (less than 0,3).
It is a very lightweight car, the most lightweight car in SUV category:
it weights 1600 km which is very important for fuel consumptions and performance.
A unique characteristics is the Q4 traction: it is an assisted traction because normally it is rear wheel drive but in some conditions it switches to four wheel drive.
Now, let's present this beautiful car: Alfa Romeo Stelvio.
-------------------------------------------
Mercedes-Benz A-Klasse A 160 "My First Star Pluspakket" Achteruit-RijCamera - Duration: 1:00.
-------------------------------------------
A Quiet Peaceful Debt | Original song by Deaf Cage (Demo version) - Duration: 2:17.
Well the blood keeps on flowing
Maturity's waning thin
Just like the train keeps on rolling
Down the tracks to the end
It's all the same. For the wealth to gain
You sign your name and life away
And hope and pray that you'll be saved
Before the day that comes when
you'll loose it all
You'll loose it all
Well the wind keep on blowing
The desert's scream for rain
Just like the riders still approaching
Suffering drought, heartbreak, and pain
The time comes when you can't run
from the things you've done anymore
It's overdue. The horrid truth
Endlessly pursues to settle the score
Before all is lost
Before all is lost
The reaper's harvested what you've sewn
Frayed nerves are caving in
Just like the world on your shoulders
Your head begins to spin
Your sight is blurry. You're lost in worry
The controversy's got you loosing faith
You took the risk, now abandon ship
Left to remiss resolve, 'fore it's too late
And all is lost
All is lost
Không có nhận xét nào:
Đăng nhận xét