I've been down and lost for so long But things are starting to look better
Been enclosed for a while But this heart slowly unbinds
Uncertainty, despair, and hopelessness The traces of yesterday
Will I ever overcome Will I ever make it through
One thing I know You are my breakthrough
This reflection in the mirror Covered and filled with dishonesty
I'm letting it go This portrait of my past
Goodbye Goodbye
You heal me By bringing purpose back to my life
This suffocating heart Finally breathes again
Goodbye, so long The traces of yesterday
Will I ever overcome Will I ever make it through
One thing I know You are my breakthrough
This reflection in the mirror Covered and filled with dishonesty
I'm letting it go This portrait of my past
Goodbye Goodbye
Goodbye Goodbye
The meaning of life The beauty of time
And the blues in the sky Finally unfold themselves
The purposeless days In haze
And agonizing pain Are fading away
Goodbye Goodbye
Goodbye Goodbye(Better days are coming)
Goodbye Goodbye
Goodbye to Goodbye
For more infomation >> [M/V] VOSIPER(보이스퍼) - Goodbye to Goodbye - Duration: 3:56.-------------------------------------------
改造DualShock4製作記【後編】世界に一つだけのアクリルボディ製自作コンをLaptop型PS4に収納せよ! DIY Game pad mods for PS4U - Duration: 26:15.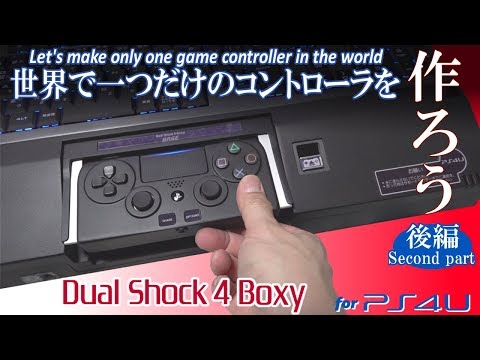
Fabrication of integrated PS4's controller (Second part)
Making a controller for housing in an integrated PS4(PS4U). It is the second part.
If you are not watching the first part, please watch it.
Yes. Last time I made around the operation panel.
I was not convinced by the tacky of around the grip. The movie ended there.
I want to do something, but after all I do not get a good idea.
There is no point in sticking to one problem for a long time, so let's proceed.
...so, I decided to leave around the stick once.
Switching feelings, relocating SHARE/OPTIONS buttons and headset jack.
Making this part
Two tact switches and a stereo jack(4pin) were soldered to the cut board.
...And, this is a self-made screw hole for fixing the board and the body.
How to make self-made screw hole.
Preparing an acrylic cylinder. It is sold at the DIY store.
Cutting it to an appropriate length ...
Bonding masking tape to the bottom.
A few drops of resin mixed powder and liquid...
In advance, a small amount of lubricated screws are inserted quickly.
Waitting for the resin to cure. It takes time because it does not touch the outside air.
After completion of curing, turn the screw and pull out. If it forgot to apply oil, it is hard to turn.
Then bond the self-made screw hole to the body.
The substrate could be fixed.
A transparent acrylic board which becomes a button is cut out. It has a button hole according to it.
Sorry for the out-of-focus blur.
This is an acrylic board with "Neck" in the center.
It is sandwiched between the body and the headset jack.
Putting a button on it.
"Neck" will tarnish, it will function like this.
...Yes. SHARE/OPTIONS buttons has been made. This ends the button surface once.
Then install a screw hole to fix the DS4 main unit and the top body.
Making a screw hole in the same way as above.
Screw hole in 5 places total.
Depending on how the button is pressed, the height of the screw hole is carefully adjusted.
Let's make side of the top body.
Making this part
First, determine the thickness of the body.
This line of L1R1 button.
Exchanging the Leutor bit for the diamond cutter.
This is expensive, but very useful.
Accuracy is not necessary now. Just cutting it.
Next is bottom. Headset Jack side panel is cut out.
The size is lazy. Later cutting and adjusting.
Jack's hole has been precisely adjusted. Now that is OK.
However...
Dimensions of the depth are determined by cutting this line.
The panel was bonded vertical to the button face. This "vertical" is not lazy.
Lazy part. High accuracy part. Learning that judgment is a way to progress.
Next, left and right sides. Docking rail guide with PS4U is necessary here.
First of all, 8 pieces of 1.5mm thick acrylic board were cut out.
Aluminum rods to serve as rails are prepared. The thickness of the aluminum rod is 3mm.
Acrylic boards are adhered to "U-shaped" so as to surround aluminum rods.
It is not hard. It is not loose. I am adjusting.
Polished with a Leutor and file...
It is the completion of the rail guide.
This incision is...
The alignment position of the rail guide.
Also determine the horizontal width according to the rail guide.
Cutting at the marked place.
The upper end makes it easier to put fingers on LR...
Cutting a little diagonally.
Panels on left and right sides.
It is bent by a soldering iron.
Adhesive left and right side · · ·
Cutting at the same height as the top.
The gaps of the panel are filled with resin. Be careful not to let the resin enter the rail guide.
Polished to prepare the surface...
The left and right side including the rail guide was made.
Next, arrange the mating surface with the bottom side body which does not exist yet.
From the marking of the cutting line, a little margin. can you see it?
"Rough surface by Leutor cutting" with this margin horizontally.
Rubbing on sandpaper.
...However, if it becomes accurate level with this, no one will suffer.
This method which is orthodox when manually leveling out...
Actually, it can not expect high accuracy.
Hand shake, internal stress, variation of friction points... The movement is very diagonal.
When expressed over, it looks like this.
For example, a frictional force applied to the front oblique with respect to the traveling direction...
It's just a car pitch movement.
That's not all.
Movement rubbing the edge by hand shake...
The horizontal is slack, the edge is round. Mechanical silhouette will be blurred.
What will happen then?
A handmade feeling appears.
When forming a face in this way, it must be careful with great care.
Therefore, the cutting surface of a new acrylic board cut off by the machine is precious. And...
I cut out the four sides around and save it for use.
This is when the handy cut surfaces are aligned.
This is when the machine cut surfaces are aligned. It is so different.
And the best new cut surface is...
Used for places where absolute accuracy can not be lost, such as seams bodies.
Seams are particularly noticeable. Especially when it becomes a large body.
There is a person who says PS4U "It seems to be a ready-made item."
I am pleased that I felt that such poverty-stricken efforts were successful.
...even so
Good...
So, this way. Processing to lazy will degrade accuracy. That.
Due to the procedural problem of making, it was impossible to use a new cut surface for this top face body. This method without any help.
··Yes. Next, the bottom body.
Making this part
Bottom body has light bar and USB with complicated structure...
...Well, what shall I do. At last the hand stopped.
The hand stopped, the sun had gone. The sun had gone by, but I am deeply thinking, so deeply...
What and where to put it. How about the procedure? How is it made?
The trigger for resumption was extraction of materials.
I decided to procure the mounter of light bar/USB unit and use it.
It would be difficult to model this...
Two acrylic boards are joined together so as to surround the extracted material.
DS4 remodeling machine Aiming at the world's thinnest, the extracted material is also being processed more compactly.
The lens cover of light bar.
The LED passes through the board.
The light bar reflector.
Temporarily assembling them...
Fitting it like this.
...With top side panel.
Since the LR button has a mechanical height, it is difficult to make it thinner any further.
...Then, next. I will continue making the side of the body.
Making this part
Here, luxuriously, using the machined surface of the example. If it can be used in the procedure of production it is done as such.
Temporarily fix 3 panels.
About horizontal with the side face of the top. That is exactly.
And its side faces are adhered to each other. Carefully not to adhere to the top body.
Adhesion is complete.
Tips is bent.
The resin is attached thickly to the joint between the panels...
Form with a Leutor and file.
The tip part bent is...
Naturally, high accuracy is not obtained by bending with a soldering iron.
Again over expression. Slightly, it is outward.
In that case, we can correct the accuracy of the bent portion by polishing it.
The tip part with such face aligned.
Next, cutting obliquely.
It is the same as the slope of this upper panel.
Carefully align the surface with the top surface body and fix it temporarily.
Adhesion is complete.
Forming an adhesive portion.
Next opening the light bar and the USB window.
Yes, it's opened.
Since the slopes of the panels are uneven, naturally, gaps are formed around this.
Shaping it to fill the gap. Adjustment in millimeters or less.
Track accuracy. That is really troublesome.
Hmm... like this.
This line becomes the total height of DS4B...
Just to be sure, the height of the side was also aligned.
A vibration motor is mounted in these spaces.
However, the other side of the feather is decorated. It becomes slightly unstable when mounted as it is.
So I made a lazy spacer. The invisible part is a tear-off work.
Processed by cutting 0.5mm thick PVC board.
While lightly adhering this to the motor with a little double-sided tape...
Apply rubber type adhesive on the front side. Resin adhesion to PVC is impossible.
Before the adhesive dries quickly it sticks to the body side.
When pulling out when the adhesive dries...
The small double-sided tape peels off, only the spacer is fixed to the body.
This is a way to complete alignment and adhesion in one go.
Method of fixing vibration motor. I made the stay and fixed the screw.
With this, the internal construction is almost done.
Let's go back to body production.
Making this part
Since the height of the periphery of the motor was also decided, we will narrow down the bottom body.
I cut it with this line.
This is an acrylic board to be the bottom plate. Cutting out to a larger size...
I will attach it to the side which its made earlier.
It is glued with too much resin.
Roughly scrape off the extra using a rutherf...
In addition, scraping with a file...
It was molded with sandpaper.
Material is not stable...
These projections seal motion.
If closed, it will be fixed like this.
A guide is provided to prevent the two bodies from shifting.
The final shape gradually became visible.
...I like this angle.
The side like a trapezoid is somewhat distinctive.
Next I will make screw holes to secure the two bodies together.
There are 4 screw holes in total.
I would like to reproduce the deep screw hole that is often seen in game controllers.
If do not do this, the finish like a product will be lost.
Acrylic cylinder cut obliquely...
Total 4 places. It is set vertical to the button face.
Enlarging the hole so that the screw passes.
Like this.
Cutting the acrylic cylinder to the same height as this surface.
Next, an acrylic board cut into a circle is prepared...
It adheres to the tip of the cylinder.
...And a hole is made so as to be the same as the diameter of the screw thread.
Looking from the front side like this.
Its deep... Do not you understand well with this?
Next is the top side body on the opposite side. This side is a scalpel screw.
A screw hole made by the example method. It is extended with an acrylic cylinder.
About the height of extension. It is necessary to adjust so that a slight gap is formed when the body is closed.
After adjusting, attach a lot of resin...
Before the resin dries, the body is closed and fixed exactly with tape.
This also performs alignment and adhesion at once.
It is completed when the resin cures.
There is one more gimmick to leave...
It is a switch that seals the vibration motor when PS4U and DS4B are integrated.
It is better not to vibrate during storage.
Making this part
Let's make a sealing switch for the vibration motor.
This is a waste material at the time of making Famicom Pocket of my mods. It is a shield board of the Game Boy.
It is thin and easy to process. Moreover, it is possible to solder. Such a shield board is useful.
Cutting out the contact point of the switch...
Combined with acrylic board, made it like this.
It usually conducts electricity.
When pressing the center switch...
The connection is cut off and electricity is not transmitted to the vibration motor.
This switch is fixed to the bottom body with claws and screws.
When integrated, this is pushed.
Also, I set a plate for scratch protection. It is in the groove provided on the bottom.
The plate is made of aluminum in this image, but it is finally changed to acrylic board.
Well, let's finish remaining wiring work...
The DS4B components are complete.
With this knowledge of the dimensions of the controller, it is finally possible to start making the PS4U body.
Various tests before that.
I will test wired communication and charging. It works properly.
Game play test on wireless.
Alright... All right! It certainly is working.
Although it seemed to be distressed many times during the production, ...it was able to achieve it.
After that, when PS4U main body is completed, I will make final molding together.
Currently, the sharp corner of the controller is stuck in my hand and it hurts! lol
He smiled innocently and said so, and then went back to the production room again to produce the PS4U body.
What is waiting for him there. It was far harder to make controller than before.
It is the days of despair wrapped up in sweat and dust and conflict. To endure, such as everyday to endure.
The date and time passed. Everyone has forgotten about him any more.
Still he came back.
But his appearance changed, the impression of that innocent smile had disappeared. And what lives in his heart...
Nmmmm-----!!
Crappy...! This molding is truly crappy.
Especially here!!
Does think that it will solve if digging all the grooves?
Bordering around the stick is effective! ...Baby knows that as well.
Use grip for 3DS! Why not utilize more ready-made items?
Hmm! ...Its got a little better. Stupid!!
Ouch...!
...brat! fought back me.
...Fought back on me with a sharp corner.
Giving an attack on me. ...not bad!
But that trifling attack made me angry. You will regret it in the afterlife.
Eat it...!
SHUN - GOKU - SAKU
The fool!!
You should have had it round like a cat from the beginning!
What?
Bored already...?
It's a setting called "Evil Kei" ...
Ah... Is not it fun? Alright.
..sorry.
Apparently, as I approached the end of editing, I tend to be desperate. Always keep in mind that before editing "I will try to edit seriously only this time"
Well, Let's go back to the real theme.
Rounding the corner by SHUN - GOKU - SAKU...no! It was molded with various files.
Like the part of the stick, the LR part of the poor texture was also bordered.
Finally small scratches and gaps. A part such as a small corner is carefully molded with resin and light curing putty.
About the work after this. That was said in a previous video of the main part.
Rinse off oil with neutral detergent...
Substrate painting.
Color painting.
Mat urethane painting.
And pasting label seal and plate.
Assemble in order...
DS4B is completed.
I tried shooting from various angles.
By the way ... There is a little supplement.
The only function that did not port to DS4B. It is the EXT terminal beside the headset jack.
Currently, it seems that the EXT terminal is used only for the charging station, so it has been omitted.
First of all, since the PS4U main unit also serves as a charging stand.
...Yes.
This time I mainly explained my work on acrylic board construction.
The invisible place is lazy. The visible place is nervous.
Allotment of such resources is a way to preserve my motivation over the long term.
Afterwards ... to go to the workbench even if disagreeable work. If skip over too much in most cases the project will be abandoned.
In short, what matters is not technology or knowledge. They are not necessary for such as cardboard craft.
If you do it several times, you get used to getting the point. It's true.
What is more important than that is the consent of the family and the feeling that will do it...
About such mental...
Eh?
What?
Ah. Is this?
This is DualShock4. Brand new.
Because I do not want to use DS4B. Because it made it with great care.
Corner will wear out if used. The stick also deteriorates.
...Yes. I'm sorry.
Finally, a recent report.
It is in the midst of buying the parts of MOD of the next work now. In this way, they arriving one after another.
Inside of this, the parts of the next and next work MOD are also mixed.
I feel troubled by the feelings just going ahead.
Other than that... After all, I bought an anniversary collection.
I pulled out arcade controller from my parents house...
...However, arcade controller for PS3 does not move perfectly.
Is this something I have to buy for PS 4 if I want to use arcade controller?
Is it appropriate to invest in additional to play this?
Every time I update the hardware I also update expensive arcade controller?
I am saddened by the public's "fighting game away", as I am, such a current situation is tough.
...That is why I am remodeling this for PS4 now.
There may not be much demand, but maybe the content of the next movie will be this.
However, arcade controller remodeling has a part suitable for the entrance of "modified hobby".
I myself used a soldering iron in places other than school classes, it was arcade controller remodeling. That is the beginning.
Certainly, I modified for Super Famicom for 3DO. After all I still wanted to play SSF2Turbo.
It is an old story for over 20 years.
I hope to create a video directed to those who wish to start such a "modified hobby".
Well then...
It got longer.
Thank you for viewing this time too.
-------------------------------------------
'Catch Me If You Can': Las Vegas Attraction Gives Drivers Hot-Pursuit Experience - Duration: 1:49.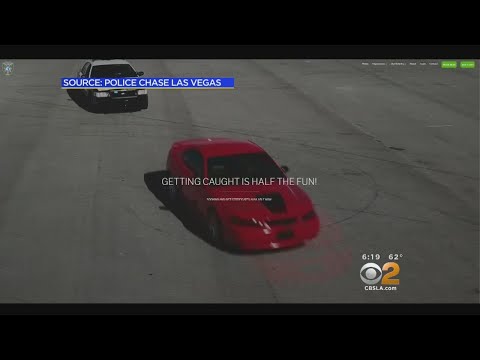
-------------------------------------------
メルセデス・ベンツ Vクラス:高速巡行時や都市高速程度の中速コーナーで見せるスタビリティの高さは、さすがメルセデス - Duration: 5:34.
-------------------------------------------
We Wish You A Merry Christmas | FOX BROADCASTING - Duration: 0:53.
-------------------------------------------
Comeback of the CENTURY! Final answer 64 points! WOW!!! | Family Feud - Duration: 5:07.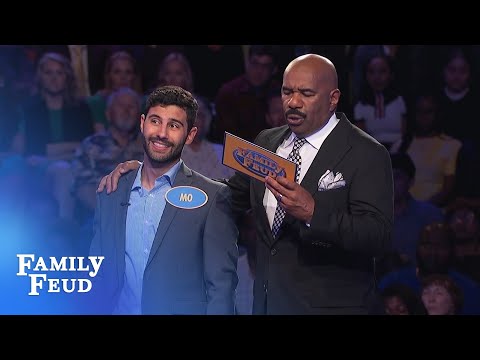
ALIA: YES!
STEVE: WELCOME BACK TO "THE
FEUD," EVERYBODY. THE FARUNIA
FAMILY WON THE GAME.
ALIA: YES! WHOO!
STEVE: AND NOW IT'S TIME TO
PLAY--
AUDIENCE: FAST MONEY!
ALIA: WHOO!
STEVE: ALL RIGHT, ALIA.
ALIA: ALIA.
STEVE: ALIA. I'M TRYING TO GET
IT, BABY.
ALIA: YOU GOT IT. YOU'RE GETTING
THERE.
STEVE: ALIA. MO IS OFFSTAGE--
I GOT THAT RIGHT, THOUGH, DIDN'T
I?
ALIA: YEAH, SURE DID.
STEVE: AIN'T BUT TWO LETTERS. MO
IS OFFSTAGE. I'M GONNA ASK YOU
5 QUESTIONS IN 20 SECONDS. IF
YOU CAN'T THINK OF SOMETHING,
YOU JUST SAY "PASS." YOU AND MO
TOGETHER COME UP WITH 200
POINTS, LOOK RIGHT THERE, TELL
THEM WHAT YOU'RE GONNA WIN.
ALIA: $20,000!
STEVE: YEAH.
ALIA: WHOO! WHOO!
STEVE: ALL RIGHT, YOU READY?
ALIA: YES.
STEVE: 20 SECONDS ON THE CLOCK,
PLEASE. HERE WE GO. ON A SCALE
OF ONE TO TEN, HOW WELL DO YOU
KNOW YOUR NEXT-DOOR NEIGHBOR?
ALIA: 4.
STEVE: NAME SOMETHING WOMEN WEAR
AT NUDIST COLONIES.
ALIA: SHOES.
STEVE: NAME A SPORT WITH A
SPECIFIC SEASON.
ALIA: FOOTBALL.
STEVE: NOW THAT YOU'RE AN ADULT,
NAME A DESSERT YOU CAN HAVE ANY
DARN TIME.
ALIA: CHEESECAKE.
STEVE: FILL IN THE BLANK. SESAME
BLANK.
ALIA: SEEDS.
[BELL DINGS]
[CHEERS AND APPLAUSE]
STEVE: ALL RIGHT, LET'S GO. ALL
RIGHT, LET'S SEE WHAT WE GOT
HERE.
ALIA: OK.
STEVE: ON A SCALE OF ONE TO TEN,
HOW WELL DO YOU KNOW YOUR
NEXT-DOOR NEIGHBOR? YOU SAID 4.
SURVEY SAYS...
OK.
ALIA: OK.
STEVE: NAME SOMETHING WOMEN WEAR
AT NUDIST COLONIES. YOU SAID
SHOES. SURVEY SAID...
NAME A SPORT WITH A SPECIFIC
SEASON. YOU SAID FOOTBALL.
SURVEY SAID...
THERE YOU GO.
ALIA: WHOO!
STEVE: NOW THAT YOU'RE AN ADULT,
NAME A DESSERT YOU COULD HAVE
ANY DARN TIME. YOU SAID
CHEESECAKE. SURVEY SAID...
ALIA: OK.
STEVE: FILL IN THE BLANK. SESAME
BLANK. YOU SAID...
ALIA: SEEDS.
STEVE: SEEDS. SURVEY SAID...
ALL RIGHT, YOU'LL BE OK.
[CHEERS AND APPLAUSE]
ALL RIGHT, COME ON, MO.
MO, HOW YOU FEELING, MAN?
MO: DOING ALL RIGHT.
STEVE: COME ON, MAN. COME ON.
MO: GOT TO REDEEM MYSELF.
STEVE: COME ON, CLEVELAND. NOW,
I GOT GOOD NEWS FOR YOU. SHE GOT
113.
MO: HOO-KAY.
STEVE: THAT'S RIGHT.
MO: THANK YOU.
STEVE: BUT YOU GOT TO GET 87.
ALL RIGHT, LET'S REMIND
EVERYBODY OF HER ANSWERS. 25
SECONDS ON THE CLOCK, PLEASE.
ON A SCALE OF ONE TO TEN, HOW
WELL DO YOU KNOW YOUR NEXT-DOOR
NEIGHBOR?
MO: 7.
STEVE: NAME SOMETHING WOMEN WEAR
AT NUDIST COLONIES.
MO: BIKINIS.
STEVE: NAME A SPORT WITH A
SPECIFIC SEASON.
MO: FOOTBALL.
STEVE: TRY AGAIN.
MO: HOCKEY.
STEVE: NAME--NOW THAT YOU'RE
AN ADULT, NAME A DESSERT YOU CAN
HAVE ANY DARN TIME.
MO: PHEW, CHEESECAKE.
STEVE: TRY AGAIN.
MO: PIE.
STEVE: FILL IN THE BLANK. SESAME
BLANK.
MO: STREET.
[BELL DINGS]
[CHEERS AND APPLAUSE]
ADAM: OK!
ALI: HE GOT IT. YOU'RE GOOD, MO.
ALIA: WHOO! OK!
STEVE: ALL RIGHT, WE NEED 87
POINTS. ON A SCALE OF ONE TO
TEN, HOW WELL DO YOU KNOW YOUR
NEXT-DOOR NEIGHBOR? YOU SAID 7.
SURVEY SAID...
MO: OK.
STEVE: 10. 10 WAS THE NUMBER ONE
ANSWER. ALL RIGHT. NAME
SOMETHING WOMEN WEAR AT NUDIST
COLONIES. YOU SAID SAME THING
THEY WEAR AT THE BEACH. SURVEY
SAID--BIKINIS.
[BUZZER]
MO: AHH.
ALIA: THAT'S OK.
STEVE: JEWELRY AND WATCH.
JEWELRY AND WATCH WAS NUMBER
ONE. 75 POINTS AWAY. NAME A
SPORT WITH A SPECIFIC SEASON.
YOU SAID HOCKEY.
SURVEY SAID...
MO: OK.
STEVE: FOOTBALL. FOOTBALL WAS
NUMBER ONE. WE NEED TWO BIG
ONES. WE'RE 64 POINTS AWAY. NOW
THAT YOU'RE AN ADULT, NAME A
DESSERT YOU CAN HAVE ANY DARN
TIME. Y'ALL MUST LOVE
CHEESECAKE, MAN.
MO: OH, YEAH.
STEVE: 'CAUSE SHE SAID
CHEESECAKE.
ALIA: YEAH.
STEVE: WOW.
ALI: THANKS, MOM.
STEVE: SURVEY SAID--YOU
SAID PIE. SURVEY SAID...
MO: OH. ICE CREAM?
STEVE: ICE CREAM WAS NUMBER ONE.
MO: ICE CREAM.
STEVE: 56 POINTS AWAY. YOU NEED
A BIG ONE.
MO: MAN.
STEVE: FILL IN THE BLANK. SESAME
BLANK. YOU SAID STREET. SURVEY
SAID...
MO: YEAH!
[CHEERS AND APPLAUSE]
STEVE: SESAME STREET WAS THE
NUMBER ONE ANSWER. WOW. WOW.
THAT'S $20,000, AND THEY'RE
COMING RIGHT BACK ON "FAMILY
FEUD." I'M STEVE HARVEY. WE'LL
SEE YOU NEXT TIME.
-------------------------------------------
Alexandria Ocasio-Cortez On Her Plans In Congress | All In | MSNBC - Duration: 8:11.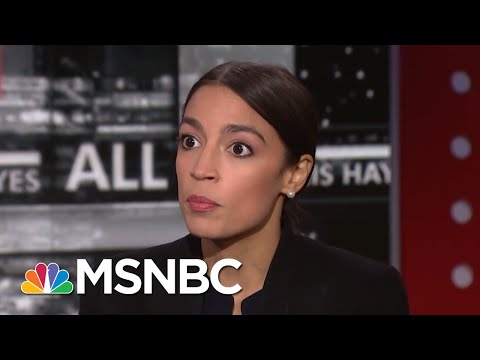
-------------------------------------------
Ex-ICE director slams Kamala Harris for comparing ICE to KKK - Duration: 5:24.
-------------------------------------------
Is Facebook deliberately causing harm to Americans? - Duration: 3:28.
-------------------------------------------
Ingraham: Time for the Uniter-in-Chief - Duration: 9:06.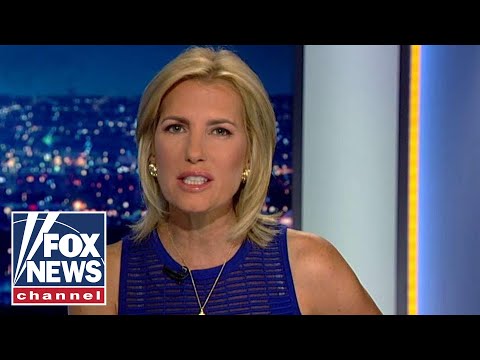
-------------------------------------------
Dan Bongino, Willie Robertson on Hollywood activism - Duration: 5:33.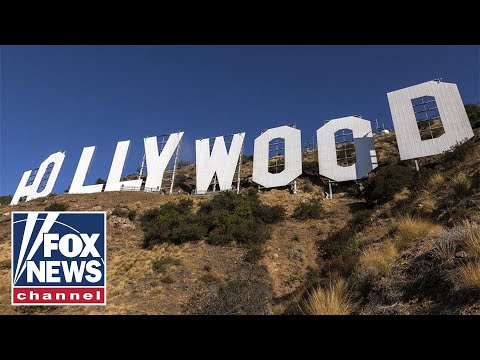
-------------------------------------------
이달의소녀탐구 #443 (LOONA TV #443) - Duration: 1:01.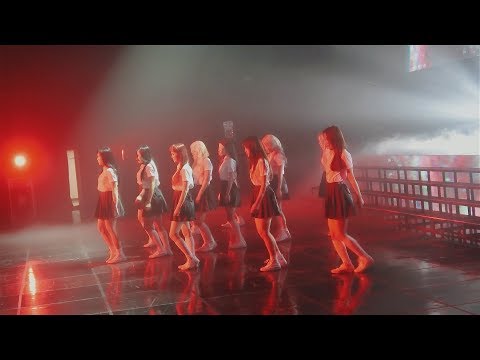
(The concert starting with 'favOriTe')
(And Orbit giving a big cheer for LOOΠΔ)
All: Hello, we're LOOΠΔ!
HaSeul: Actually I did imagine, many times, what it would look like if all the seats are taken
HaSeul: Look around now, it's magnificent~
Chuu: I'm very happy to be able to stand on this stage!
Chuu: However, actually it's little nervous~
HyunJin: Orbit, are you ready to enjoy the concert?
(Even though it's the first concert, LOOΠΔ members are comfortably communicating with Orbit!)
-------------------------------------------
4 Dead In Chicago Hospital Shooting - Duration: 1:02.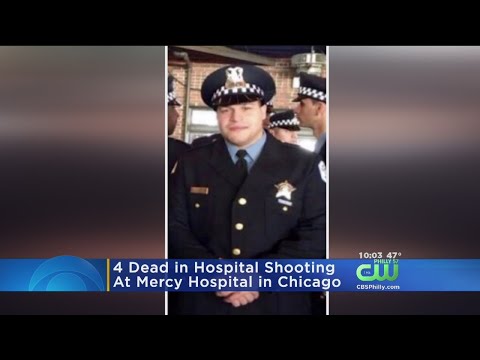
-------------------------------------------
'The Metamorphosis' Ep. 3 | My Brilliant Friend - Duration: 1:01.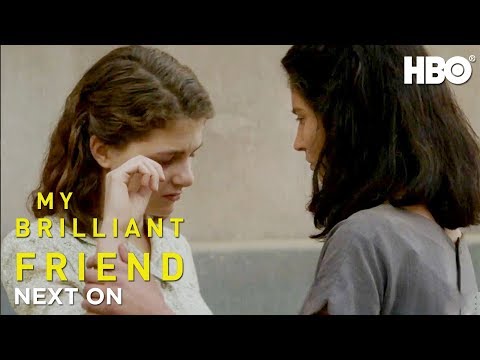
ELENA: Lila!
Lila!
♪ ("SUMMER 3" BY ALEX RICHTER ET AL. PLAYS) ♪
(SPEAKING ITALIAN)
ADULT ELENA:
-(GRUNTS) -(KNIFE CLICKS)
ELENA: No, Lila!
-------------------------------------------
고양이 대왕 문어 먹는 날 - Duration: 10:04.
Is there anything you don't eat??
You...
(Laughing)
You...
Face too~
Huh?
(Laughing)
Ahhhhh~! (Water flowing)
(Water flowing)
Let... let me wash your arms first.
(Water flowing)
Don't! It's huge~!
Oh, it's so scary~!~!
Oh~
Wow, this is so long.
DD! You should keep me safe!
Geez....
AWWWWW
HELP!
Geez... (lol)
Oh, god...
I'm the outlaw of the sea, Kraken!
KUWAAAAH~!
(Laughing)
Kyut Kyut Kyut~
(Laughing)
Only with these parts...
Kyut Kyut Kyut~
(Laughing)
Kyut!
(Laughing)
Alright then,
"I'm the outlaw of the sea, Kraken!"
KUWAHHHHH!
(Laughing)
Phew... It's heavy...
Heavy...
I'll make this completely clean!
Gonna be fine.
TT: She's doing something weird again...
Aww...head first...
(Groaning)
(Groaning)
The outlaw... of the sea...
(Groaning)
Umm... (lol)
Not sure it's washed well... (lol)
Please...
I'm sorry for...
putting you into this humble, small place... (lol)
Don't lick it, kitty! Oh...
Geez... My waist...
I think it's heavier than DD...
(Groaning)
BAMM!
Take... take the head out and...
Which part of it is the head??
Take the head out and...
get rid of the ink sac...
Are you interested in it, TT? I'll cook it.
(lol) She smacked her lips!
How did you know it's food??
(Laughing)
The outlaw of the sea!
KUWAHHHH!
(Laughing)
KUWAHHHH!
(Laughing)
Sniff sniff!
No, just smell it.
Geez...
(Groaning)
Ta-da!
AWWW....
Anyway,
I gotta get rid of the ink sac first before cooking it.
It won't take that long, kitty.
Gotta take the head out...
But how...?
(Embarrassed)
NO!
AAAHHHHHH!
It bursted!!!!!
YUCK! Geez!
AHHH!
(Washing)
(Embarrassed)
Move away! Move away! I'll put the knife away!
AH~~~~
I feel dizzy...
(Groaning)
(Groaning)
Grab the head and...
(Groaning)
put legs into...
Huh?
Legs first! Ugh~
It's got too much wet...
(Groaning)
Put legs into it! In and out!
(Groaning)
Legs curled up well, by the way. Awww..
Good. I think it's enough.
One, two... UP!
OK. Go down, please.
Phew...
Good.
Good!
The lid!
Then, I'll see you soon.
Phew...
Hello? It's the butler.
Oh... It's looks a bit... scary.
It's time to get in the cold water.
I got gloves since you look so hot.
Ooh....
I think...
the head looks under cooked though...
Ah.. This way...
(Laughing)
How can I cut it...?
Oops, come up to the cutting board.
Are you interested in it?
(Laughing)
I'll cut it for you, kitties.
Don't eat too much!
(Laughing)
Does it look yummy?
Oh, it's good~
(Laughing)
(Laughing)
I gotta cut it first, kitty.
You don't wanna eat this, Lulu?? Wow...
Lulu doesn't eat sea food these days...
Nope. The back part of it is mine.
Eat the tip part. (lol)
Shoo~ Shoo~ Shoo~
OK~
Ta-da!
Oh, it looks so nice!
This is mine~ ♬
Ta-da!
Lulu, where are you going?
Lulu: Uh...
Lulu: I think I can wait here.
Really?
Only Lala is coming bravely.
EHBI! (Surprise)
(Laughing)
Are you not even scared?
I'll cut it for you.
Lala, I'll cut it before I give you.
Almost done...
(Cutting)
You... (lol)
How an earth could you do that, kitty?
Let me wash my hands...
YOU!
(Cutting)
(Laughing)
Are you gonna eat all of this? You little?
Wow. I told you to wait
until I cut this, huh? (lol)
(Laughing)
Wow...
Let me cut this. Hold on.
Oh~ Do you like it , Chuchu?
You too, chairman Momo?
What about you, doctor Coco?
Shoot~!
What do you say?
You appear wherever I go, chairman Momo.
Lala already ate this much. (lol)
(Laughing)
Chairman Momo is targeting the bottom of it,
and doctor Coco is targeting the top. (lol)
Hi, Lala!
(Laughing)
How is it?
You're amazing, kitty.
How could you do this, you little kitty?
Ta-da!
It's snapped!
(Laughing)
Is there anything you don't eat??
You...
(Laughing)
You...
Hey... Oops...
(Laughing)
I'll go cut it.
Stop! Stop!
I'll mince it for you.
Look!
YAP!
I'm not the one I'm used to be any longer!
Lulu: It's too noisy!
DD: (Cat food-ist)
-------------------------------------------
Stacey Abrams: 'It Was Not A Free And Fair Election' | All In | MSNBC - Duration: 7:32.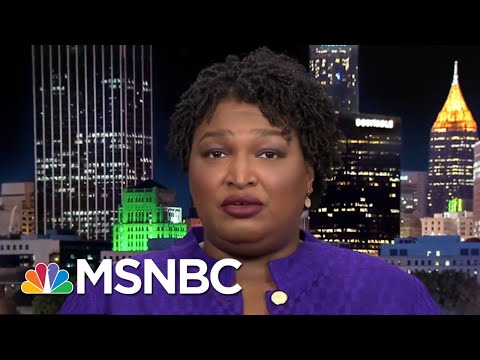
-------------------------------------------
The National for Monday, November 19, 2018 — St. Michael's Charges, Canada Post, Medication Shortage - Duration: 1:04:48.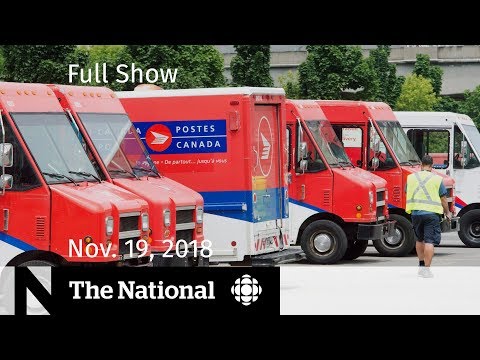
-------------------------------------------
Grow Bolder Docuseries: Hannah - Duration: 2:23.
I was sleeping 20 hours a day
When I said I was doing nothing before this I mean nothing
most people that have what I have
They're either dead or they're not doing anything
I was six years old at that time my gut was shut down
My heart was enlarged and my liver and organs were shutting down. My body is actually
cannibalizing itself
We started flying around all over the country to all these big doctor places and no one knew what was wrong.
So here was when I first got my g-tube and it runs thru me 24/7 and to my stomach
It was just to keep my blood sugar stable is just to keep me going. I wasn't supposed to get better
They thought in probably nine to twelve months I'd just check out
Like when I was nine years old, I got a Make-A-Wish trip and people were like 'oh, that's so cool a Make-A-Wish trip.'
When I was 10 or 11, I started saying that I just got a free trip for nothing because I'm still alive
So when I started out cycling for one thing I was 13 and a half and had tubes coming out of my body
The more they kept telling me I couldn't it made me just want to try that much harder
The first 10 days of learning to ride a bike. I did 210 miles
Always wanted a trophy growing up and I never wanted one just like a participation trophy or good job trophy
Like I actually wanted to earn it.
I want to be a pro and I want to be an Olympian.
I never had a happy place. That's why it's therapeutic to me
Doesn't matter what age you are, it's what you do with your life that actually makes it cool
This is just the beginning of of Hannah Jordan
-------------------------------------------
Grow Bolder Docuseries: Charlotte - Duration: 2:31.
It's just so amazing seeing those little kids
who have gone through what I've gone through, be happy and excited.
My favorite part of really the whole doll is
not the fabrics, not sewing it, but giving it to a kid.
I was born with a cleft lip and palate
so I spend a lot of time having surgeries.
I've had enough to know that they are scary.
Having that strength to go into surgery and
to not be scared to say I have my doll with me,
it's gonna be okay.
I made my first doll out of my baby clothes.
That doll means a lot to me because it is me.
It has the stitches that I have on my lip on her lip.
When I add these stitches to the doll,
that's what really makes it personal for those kids.
Like for baby Quinn,
we would add stitches here
because she has stitches in real life here.
That's the really big idea behind Stitches by Charlotte.
Yeah you might have a scar,
but it's not branding you,
it's not labeling you you can be whatever you want to be like my doll. She could be anything.
Feet are really difficult because you have to get that really nice curve.
That's a good curve.
I love being a kid, I am a kid. So I love to go swimming
I love to read, I do my homework every day for school
But when I have free time, this is what I choose to do. I choose to make dolls.
I feel like I'm on top of the world when I see a kid holding my doll and smiling.
It makes me so happy. I got a little photo from Bryson's mom saying
Bryson had a bad day full of seizures and this is where I found him tonight.
He was cuddled up with his doll in his arms.
My superpower I guess would be to make people smile,
because that I do a lot.
-------------------------------------------
When You Call Shownu - Duration: 3:03.
Hi, how are you?
Nice to meet you, I'm Shownu
I'm 27 years old
My position is vocal
My hometown is Seoul
I lived in Uijeongbu for about 10 years
I grew up in Seoul when I was in middle school
When I was young, I swam a lot
I thought it was fun when I won an award in front of my friends
I wanted to do music while I did swimming
I was at a training camp for swimming when Rain first made his debut
Seeing that, I thought, "He's so cool"
"I want to be like that, too"
That's how I started
When I was young, I never thought in detail how I wanted to succeed
But right now, just as I'm achieving new things,
I'm coming to realize that I'm also experiencing new things
There's not a big difference in how I view success now
The important thing is to keep progressing
After I've practiced more
I would like to collaborate with Bruno Mars
It's probably the feeling that MONSTA X gives off
and the energy they see in us
I want to be a singer for a long time, healthy and happy
Thank you for coming and cheering for us
We were able to have fun performing with good energy
Thanks for your support and love
So I'm doing my best always because of you guys
Thank you
Can we hide this cable behind him?
Do I have to start from "how are you" again?
-------------------------------------------
心理测试:4面墙,哪面墙后有惊喜?秒测你会有什么东西失而复得 - Duration: 7:24.
-------------------------------------------
"失望の年"ドイツはUNL未勝利、W杯準優勝のクロアチアもリーグBへ降格 - Duration: 2:45.
-------------------------------------------
[QHD] 배틀필드5 초보자를 위한 24가지 꿀팁 및 가이드 - Duration: 14:16.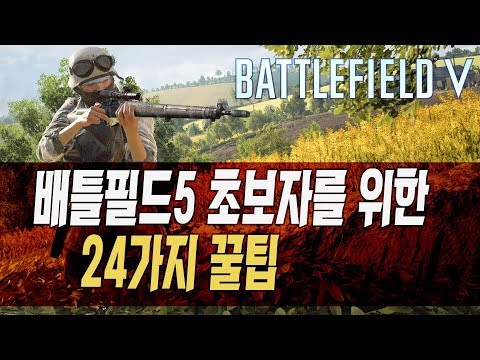
-------------------------------------------
中国新型核潜艇获四大升级 是亚洲最强水下战力 可保护094安全 - Duration: 5:15.
-------------------------------------------
Jordan B Peterson: Entrevista con GQ SUBTITULADA - Duration: 13:33.
-------------------------------------------
FREE SERIES Get your life & home organised | Part 1 - 3 Quick tips on how to get organised - Duration: 3:44.
Hi I'm Stacey and welcome to part 1 of Busy Mum's Get Organised.
I know you are VERY Busy so I will keep it short so you don't get too overwhelmed...
This video will give you a couple of quick tips to get you started on your organisational
journey.
If there is only 1 thing you do today I want you to go make your bed!
Yep that's right make your bed.
If you are already in the habit of doing this each morning then you are already ahead.
Well Done!!
If you don't make your bed each day then today is Day 1 of creating this new habit!
You will find that if your bed is clear of clothes and mess and is made up every morning
each time you walk into your bedroom you feel like you have achieved something in the day.
The next tip I wish to share with you is my all time favourite and BEST EVER TIP.
So listen up!!
Here it is.....
...... I NEVER leave a room empty handed!
That's right, before you leave a room have a quick look and to see if anything needs
to be removed and taken to a different room.... pick it up.
You will be surprised at how much actually gets put away with this very simple method
every day.
For example....
Do you have dirty laundry just thrown on the floor that needs to go to the washing hamper?
Take them to the laundry.
Now when you are in the laundry is there just 1 thing (pile of clean kids clothes folded
ready to put away perhaps?
Are you heading to the baby's room to change a nappy or pop bubs down for a nap?
Take the clothes and pop them away.
Now you are in bubs room look around just 1 thing to go to the next room ....and on
it goes.
Each room you visit.
Just 1 small thing.
Don't go overboard small steps everyday means larger amounts gets done by the end of the
week.
Now..
If you are anything like me I tend to wear the same sweatpants and hoodie for a few days
if I am just around the house.
Sometimes if I have changed for just a few hours I don't want to put the clothes away.
(Or find I am rather lazy to put them away) But I also don't want them piled on the bed,
on top of the drawers or hanging over chairs looking unsightly in the bedroom.
That's where I have 2 spare drawers.
1 by the bed side and 1 in the walk-in.
In the bedside drawer I stuff my dressing gown and pjs.
The walk-in robe draw is for worn clothed I can wear again.
This really helps out with the "lazy dumping".
I have also done the same in the kids bed room, and taught them not to get clean clothes
out until they check if they have previously worn ones they can use.
Ok, so I hope this has given you some quick tips on getting motivated.
Don't forget to comment below and let us know why and what you are struggling with to get
organised.
Recap!
So today was pretty simple right?
1.
Comment below and share your challenges.
2.
Make your bed!
3.
NEVER leave a room empty handed.
4.
Clear some drawers to pop away the clothing piles.
Told you it was short!
Thanks for watching now off you go and make that bed!
Don't forget to subscribe so your notified when part 2 is available to get more hints,
tips & hacks on getting organised.
"Wallpaper" Kevin MacLeod (incompetech.com)Licensed under Creative Commons: By Attribution 3.0http://creativecommons.org/licenses/by/3.0/
-------------------------------------------
Is a Behavior Violating Community? - Duration: 2:53.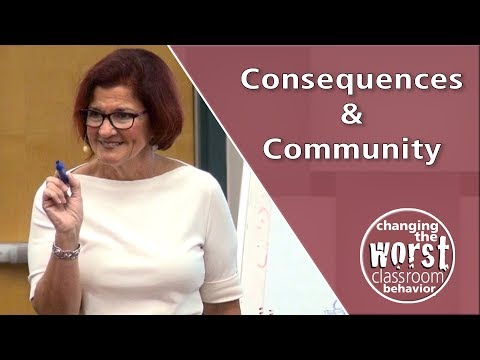
The action is let's say making noises
All right
What is making noise is defined under disruption disrespect refusal and safety. It's a disruption
So
This is kind of cause and effect. All right
You made noises
Created a disruption which violated one of your school's values?
Right off the top. What's one of the school values that you guys worked on that you think about?
Okay community you violated community which is one of our schools and our classroom values
Remember your school might not under a set of values, but your classroom can
All right. So your classroom operates under community community means that I am able to recognize when my actions impact others and
When I may have created a disruption I didn't do that
So I violated community
so now
I've got to figure out how to make that better
so I assign a consequence I
The adult what's a consequence for disruption that violates community?
Giving back to community
So it may be some sort of restitution
Giving back I
Will have kids clean up a mess that was made by a science experiment
I will have kids take five minutes away from their choice or free time to dismantle a bulletin board that needs to be dismantled. I
Will ask other teachers in the building. I will ask all my teachers
Please make a list of all things that you need to done
things jobs that need to be done in this building in these hallways in this community and
Those are things that I use for consequences and you know
What else I find out sometimes is that the kids like that and now I know exactly why they created the disruption
What was the function of that behavior to?
Get noticed to get attention
So now I know I can in the future I figure out this is a kid who actually me
Some sort of regular community doesn't fit in so I keep working on that to reduce the level of disruption
So they don't have to use disruption to get that attention. So sometimes the consequence gives us a lot of information
So we related back to our value and so forth so think about the consequence we like all it
Thanks for watching and I hope you found this video helpful
If you did make sure to LIKE and subscribe so you can never miss another video
I speak in consult on school behavior, and I love to help districts solve some of these problems
See you next time
-------------------------------------------
Rangoli for Kartik Purnima | 7 to 4 Dots Rangoli Dakua [Rangoli for Tulasi Pooja] - Duration: 3:27.
Simple Rangoli Designs, Please Subscribe to Our Channel for More Videos
Rangoli for Kartik Purnima
7 to 4 Dots Rangoli Dakua
Rangoli for Tulasi Pooja
Rangoli Designs by Aishwarya
-------------------------------------------
Salen CUARTA y QUINTA Caravana Migrante desde El Salvador #Tijuana #CaravanaMigrante - Duration: 1:47.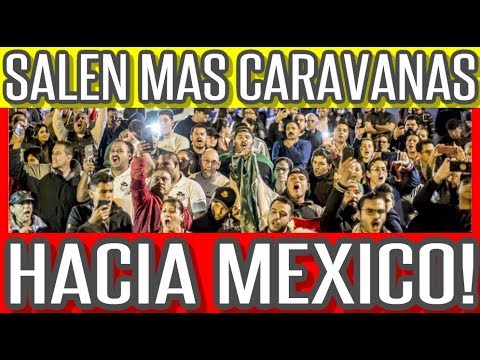
-------------------------------------------
For more infomation >> Salen CUARTA y QUINTA Caravana Migrante desde El Salvador #Tijuana #CaravanaMigrante - Duration: 1:47.-------------------------------------------
HSN | The Monday Night Show with Adam Freeman 11.19.2018 - 08 PM - Duration: 1:00:01.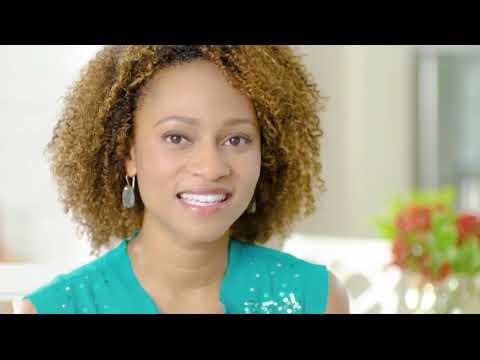
-------------------------------------------
For more infomation >> HSN | The Monday Night Show with Adam Freeman 11.19.2018 - 08 PM - Duration: 1:00:01.-------------------------------------------
🇸🇳🔴 EN DIRECT / LIVE. SÉNÉGAL (F) - CHINE (F) COUPE DU MONDE (F) - Duration: 1:21.
-------------------------------------------
For more infomation >> 🇸🇳🔴 EN DIRECT / LIVE. SÉNÉGAL (F) - CHINE (F) COUPE DU MONDE (F) - Duration: 1:21.-------------------------------------------
[M/V] VOSIPER(보이스퍼) - Goodbye to Goodbye - Duration: 3:56.
I've been down and lost for so long But things are starting to look better
Been enclosed for a while But this heart slowly unbinds
Uncertainty, despair, and hopelessness The traces of yesterday
Will I ever overcome Will I ever make it through
One thing I know You are my breakthrough
This reflection in the mirror Covered and filled with dishonesty
I'm letting it go This portrait of my past
Goodbye Goodbye
You heal me By bringing purpose back to my life
This suffocating heart Finally breathes again
Goodbye, so long The traces of yesterday
Will I ever overcome Will I ever make it through
One thing I know You are my breakthrough
This reflection in the mirror Covered and filled with dishonesty
I'm letting it go This portrait of my past
Goodbye Goodbye
Goodbye Goodbye
The meaning of life The beauty of time
And the blues in the sky Finally unfold themselves
The purposeless days In haze
And agonizing pain Are fading away
Goodbye Goodbye
Goodbye Goodbye(Better days are coming)
Goodbye Goodbye
Goodbye to Goodbye
-------------------------------------------
THANKSGIVING: THE THREE THINGS I'M THANKFUL FOR | TheDailyFA 024 - Duration: 3:48.
It gets me thinking about, you know, it's the whole,
the thankful season and what do you want to be thankful for?
What are you thankful for?
So, I thought I'd pose that question to you today.
You know, shoot it in the comments below.
What are you thankful for this Thanksgiving season?
So we're gonna walk around a little bit while we're chatting
today, enjoy the weather outside because tomorrow I'm
going on a vacation to Arizona and gonna sit by the pool
for Thanksgiving so it's gonna be a little different
from here so, I'm very excited.
Alright two things: if you can like, comment, subscribe
to this video that'd be fantastic, also if you wanna get
these videos in your email and some free guides about
how to be a more effective financial advisor,
you gotta text DailyFA to 44222.
So DailyFA to 44222, we'll get you all set up,
everything'll come right to you.
So Chicagoans, they're kinda mad right now.
And it's all due to this weather here.
We're used to this weather in the winter,
but not this early.
Like Thanksgiving is not until next week and
we're not too happy.
But it gets me thinking about, you know, it's the whole,
the thankful season and what do you want to be thankful for?
What are you thankful for?
So, I thought I'd pose that question to you today.
You know, shoot it in the comments below.
Now as I'm thinking about it, I come up with three things.
And first one is Freedom.
You know, I run my own business, I'm involved in a couple
others, and I'm not bound by an employer, I'm not bound
by anything that I have to do.
I'm free to do whatever I want to.
I'm free to partner up with people, I'm free to run any
marketing, I'm free to sign on any client I want to, or
design my business any way I want to.
It's quite beautiful in how that's set up.
And I don't take any of that for granted.
Second thing that I'm grateful for, and we're gonna
try not to get hit by a snowplow, is Opportunities.
You know, I'm free to do all these things, but sometimes
those things don't come up.
You gotta work for Opportunities.
You gotta work for things to, you know, appear.
You know, it takes time for business Opportunities
to come around and they come around by relationships.
So, building relationships is important if you
want those Opportunities to come.
And I'm thankfully, after five years
of building relationships, getting a lot of Opportunities,
and when people ask, you know, how do you this and
how do you do that, it's time and relationships,
and that gets you Opportunities.
The last thing, and this is almost the reverse, is I'm
thankful for being held Accountable.
I have to earn an income for my family.
And if this Freedom and Opportunity
don't equal income, then-
This journey doesn't work.
You know I have to generate an income for my kids, my wife,
and those Opportunities have to be right, the Freedom
has to result in something fruitful, because at the end
of the day I'm Accountable and I love it.
So enjoy your Thanksgiving, hopefully your weather's
a little better than this, and I will see you by the pool.
Take care.
-------------------------------------------
[QHD] 배틀필드5 초보자를 위한 24가지 꿀팁 및 가이드 - Duration: 14:16.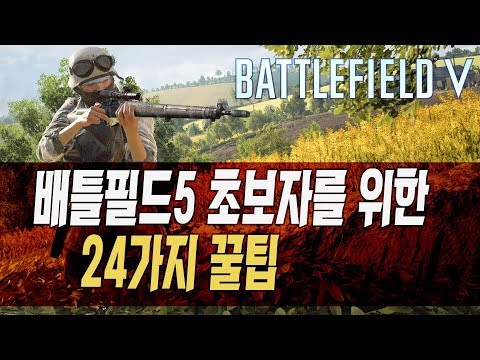
-------------------------------------------
Portal Stories mel - Duration: 40:02.
-------------------------------------------
Kevin Durant Tells Fan To Shut The Fuc* Up | Heavy.com - Duration: 3:18.
Kevin Durant Tells Fan To Shut The Fuc* Up | Heavy.com
Kevin Durant is the talk of the NBA.
Last week, he and Golden State Warriors teammate, Draymond Green get into a verbal spat.
It seems that KD had another verbal spat over the weekend in Dallas to shut the *BLANK* up!.
KD is in every news cycle these days.
Yahoo Sports' Chris Haynes, Draymond Green told Durant last Monday: "You're a bitch and you know you're a bitch.".
Green later blurted to Durant something along the lines of, "We don't need you.
We won without you. Leave.".
Haynes also noted that what ultimately led to Green's suspension was a remark in which he dared Durant to bolt in free agency next summer.
All of this occured after Green and Durant had a verbal exchange on the bench that needed to be mediated between Klay Thompson and Andre Iguodala.
In the heated exchange between KD and Dray, Durant was incensed that Green didn't pass him the ball in the final seconds of the 4th quarter for a chance to beat the Clippers in regulation.
the Los Angeles Clippers won the game 121-116 in overtime.
Durant did have a hot-hand.
He finished the game with 33 points, 11 rebounds, 10 assists, and two blocks.
Durant is also rumored to be joining LeBron James and the Los Angeles Lakers next season.
James' decision to join the Lakers this offseason wasn't a surprise and it is expected that the Lakers will try to add another superstar to play alongside him.
James signed a four-year, $153-plus million deal with the Lakers, via Spotrac, which features a player option for the 2021-22 season.
If Durant were to sign with the Los Angeles Lakers next offseason, it would leave them a minimum of two years to play together.
-------------------------------------------
FREE SERIES Get your life & home organised | Part 1 - 3 Quick tips on how to get organised - Duration: 3:44.
Hi I'm Stacey and welcome to part 1 of Busy Mum's Get Organised.
I know you are VERY Busy so I will keep it short so you don't get too overwhelmed...
This video will give you a couple of quick tips to get you started on your organisational
journey.
If there is only 1 thing you do today I want you to go make your bed!
Yep that's right make your bed.
If you are already in the habit of doing this each morning then you are already ahead.
Well Done!!
If you don't make your bed each day then today is Day 1 of creating this new habit!
You will find that if your bed is clear of clothes and mess and is made up every morning
each time you walk into your bedroom you feel like you have achieved something in the day.
The next tip I wish to share with you is my all time favourite and BEST EVER TIP.
So listen up!!
Here it is.....
...... I NEVER leave a room empty handed!
That's right, before you leave a room have a quick look and to see if anything needs
to be removed and taken to a different room.... pick it up.
You will be surprised at how much actually gets put away with this very simple method
every day.
For example....
Do you have dirty laundry just thrown on the floor that needs to go to the washing hamper?
Take them to the laundry.
Now when you are in the laundry is there just 1 thing (pile of clean kids clothes folded
ready to put away perhaps?
Are you heading to the baby's room to change a nappy or pop bubs down for a nap?
Take the clothes and pop them away.
Now you are in bubs room look around just 1 thing to go to the next room ....and on
it goes.
Each room you visit.
Just 1 small thing.
Don't go overboard small steps everyday means larger amounts gets done by the end of the
week.
Now..
If you are anything like me I tend to wear the same sweatpants and hoodie for a few days
if I am just around the house.
Sometimes if I have changed for just a few hours I don't want to put the clothes away.
(Or find I am rather lazy to put them away) But I also don't want them piled on the bed,
on top of the drawers or hanging over chairs looking unsightly in the bedroom.
That's where I have 2 spare drawers.
1 by the bed side and 1 in the walk-in.
In the bedside drawer I stuff my dressing gown and pjs.
The walk-in robe draw is for worn clothed I can wear again.
This really helps out with the "lazy dumping".
I have also done the same in the kids bed room, and taught them not to get clean clothes
out until they check if they have previously worn ones they can use.
Ok, so I hope this has given you some quick tips on getting motivated.
Don't forget to comment below and let us know why and what you are struggling with to get
organised.
Recap!
So today was pretty simple right?
1.
Comment below and share your challenges.
2.
Make your bed!
3.
NEVER leave a room empty handed.
4.
Clear some drawers to pop away the clothing piles.
Told you it was short!
Thanks for watching now off you go and make that bed!
Don't forget to subscribe so your notified when part 2 is available to get more hints,
tips & hacks on getting organised.
"Wallpaper" Kevin MacLeod (incompetech.com)Licensed under Creative Commons: By Attribution 3.0http://creativecommons.org/licenses/by/3.0/
-------------------------------------------
Salud - Depresión en Adultos Mayores - Duration: 2:57.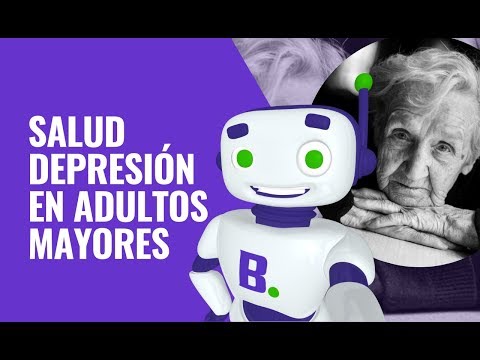
-------------------------------------------
汪小菲深夜发文:她是两个孩子的妈唐嫣大S同框被指差距大 - Duration: 5:26.
-------------------------------------------
Chelsea vs Everton on TV: What channel is Chelsea vs Everton on today? - Duration: 3:06.
Chelsea star Eden Hazard has spoken out about the rough treatment doled out by his opponents ahead of the clash with Everton this afternoon
"I am not happy to be fair, but it's part of football," Hazard said. "The referee tries to do his job and I try to do mine
I guess when I am on the floor I can win free-kicks so every free-kick with Chelsea is a chance to score more goals
"I'm 27 now and starting to get older, so I have to take more care of my body. "I am feeling the wear and tear
I have been playing football as a professional for more than 10 years now. It is part of the game, I guess
"I will just start with more treatment and training. I have been doing yoga since I have been at Chelsea
"Chelsea vs Everton - how to watch The Premier League clash will be shown live on Sky Sports Main Event and Sky Sports Premier League
Pre-match coverage gets underway at 1pm ahead of kick-off at 2.15pm. Existing Sky Sports customers will be able to stream the action via the Sky Go app, which can be downloaded across a host of devices
Fans without a subscription can still live stream the match by purchasing a NOW TV sports pass
Day Passes start at £7.99 and give you 24 hours of access to Sky Sports channels without locking into a contract
Chelsea vs Everton team news Chelsea: Arrizabalaga, Azpilicueta, Rudiger, Luiz, Alonso, Kante, Jorginho, Kovacic, Willian, Morata, Hazard
Subs: Fabregas, Caballero, Giroud, Zappacosta, Christensen, Barkley, Pedro. Everton: Pickford, Coleman, Keane, Mina, Digne, Andre Gomes, Gueye, Walcott, Sigurdsson, Bernard, Richarlison
Subs: Baines, Jagielka, Tosun, Stekelenburg, Davies, Calvert-Lewin, Lookman.Chelsea vs Everton latest odds Chelsea 4/11 Draw 4/1 Everton 8/1 (Odds courtesy of Betfair)
-------------------------------------------
ENG CC] 신부 웨딩 셀프 스탬핑 네일아트 단아한 블링블링 디자인 | 2018 Bridal Wedding Self Nails - DIY - Stamp Nail Art - Duration: 6:35.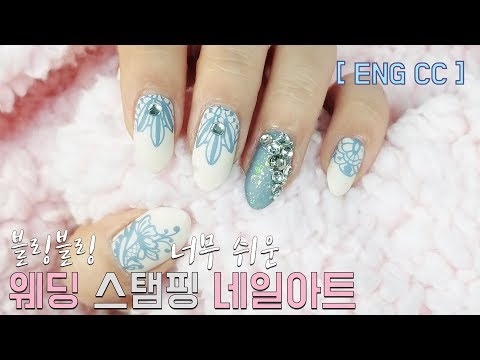
The stamp plate that I will use today is
called "Fancy Lover 01" from Pueen
and I used this plate
on the last video for French style nail art.
There are a lot of beautiful images
on this plate
so I will use this plate again
for wedding bridal nail art.
Shall we start?
Apply your favorite base coat first.
I'm using CND sticky base coat now.
I will use these two nail polish colors
to make a good match with
white wedding dress.
They will bring out soft yet classy nail design.
This classy gray color is a 'Greycian Goddess' from L'oreal
and this soft light pink color
is a 'Be There in a Prosecco' from O.P.I.
I will apply gray color only on my ring finger nail.
I will wear 2 coats for today's polishes.
I just finished with applying 2 coats of polishes.
Now, I am waiting for my nails to get dry
for a couple minutes.
While I am waiting,
I put some liquid latex on my fingers.
Ok, let's play with stamp plate!
I'm gonna use this
blue gray colored nail stamping polish
to match with my ring finger color.
I will use a clear stamper today
since I need to see exactly where
my image is landing on my nails.
For my middle finger,
I stamp this image on my nail
I repeat the same image on my index finger nail.
This image is a perfect size for my pinky nail.
All images on this plate have pretty thick lines
so I won't cover my whole nail with stamping
but leave some space
to show this beautiful creamy pink color.
Now let me stamp this flower image for my thumb nail.
Now it is time to attach some
sparkling crystal rhinestones.
I'm gonna use 3 different top coats today.
The first one is a great top coat for stamping nails
and it prevents stamped images from smearing.
I will apply rhinestones on my middle and index finger nails.
I want my ring finger nail to look fancy
so I will apply this hologram powder
from Born Pretty onto my nail
to give more shine on the background color.
I apply same top coat over the hologram powder
and before it gets dry,
I place some crystal
and caviar beads diagonally on the nail.
The second top coat that I will use today is
Seche Vite
and I apply this for all of my nails
to seal crystal rhinestones.
Now take liquid latex off
and clean my fingers with 100% pure acetone.
The last top coat is a matte top coat
and it will give my nails a softer look.
This top coat instantly transforms my nails into a matte
finish right after I apply.
I shouldn't touch
crystal beads with this matte brush
so carefully apply without touching crystals.
I love this matte finish with today's design.
How is it?
The matte finish gives different feelings from the shiny finish, right?
The matte finish is definitely a good choice
for today's bridal wedding nail art.
I focus on wedding themed nail art today
but I think it is also good to wear casually.
I really wish you to try fun
and easy stamp nail art!
-------------------------------------------
Liverpool news: Reds hero reveals 'big problem', Jurgen Klopp set Premier League challenge - Duration: 3:12.
Liverpool are unbeaten through the opening 12 matches of the Premier League, but still don't sit top of the table
Reigning champions Manchester City are also unbeaten, as are Maurizio Sarri's Chelsea
Liverpool were tipped to be the closest challengers to Pep Guardiola's side this season, but have struggled to find their best form despite the unbeaten start
The Anfield outfit have never won the title in the Premier League era, with their last trophy coming in the League Cup in 2012
And Fowler believes Klopp needs a trophy for this season to be successful though admits City provide the biggest block in that quest
"A gauge is getting as high up in the league as they can," Fowler told Sky Sports' The Debate
"As much as we talk about Liverpool being this unbelievable side who are easy on the eye and great to watch, there comes a time when you need to start winning stuff
"I think Jurgen Klopp's getting together a great, great squad but I think one of the problems we have is Manchester City are brilliant
"That's one of the big problems. You can get a wonderful side put together but you've got to try and catch them and then hang onto their coat tails
"For me, no [finishing in the top four isn't enough]. "It really isn't because I'm not one of these fans that think you should be celebrating finishing fourth
"I think a chairman or the owners should be the ones celebrating. For me that's celebrating mediocrity
I've always wanted to win stuff. "I wanted to be remembered for what trophies I won as opposed to where I finished in the league
"I understand why clubs are happy finishing in the top four but I think a club the size of Liverpool's stature should be finishing in the top four all the time anyway
"As I said before, there comes a time when you need to win a trophy. I don't care if it's a League Cup
People will belittle that but I've won one, it's a brilliant trophy. "When you think of football in terms of what you can win there's an FA Cup, a League Cup, the Premier League and the Champions League
There are only four trophies so it's tough."
Không có nhận xét nào:
Đăng nhận xét