What's up everyone?
My name is John, and this is the Wrestling Report.
First up, we have some news about Kurt Angle returning to WWE.
Reports are now claiming that Angle has been telling promoters that he can't take any
more independent bookings, because he will be coming back to WWE in April.
Of course, everyone has the right to be skeptical about the Olympic gold medalist making his
comeback, as there are rumors of WWE possibly wanting to keep Angle out of the company due
to his past issues with drug addiction.
At the very least, it looks as though Kurt is ready to make his return.
Next up, it seems as though Smackdown Live has finally done it, because Smackdown had
a higher number of viewers this week than Monday Night Raw.
With the promotion of three title matches and the return of John Cena, the blue brand
was able to pull ahead by about 30,000 viewers.
This week's show also brought in a whopping 200,000 more viewers than the week before,
which is an incredible way to close out 2016.
Finally, it appears as though AJ Styles might just retain his championship at the Royal
Rumble, as he is now being advertised to defend his WWE championship at a live event after
the Rumble.
This match will take place against Dean Ambrose with James Ellsworth as the time keeper, and
the show will also feature an Intercontinental title match between The Miz and Dolph Ziggler.
What do you think is going to happen between AJ Styles and John Cena at the Royal Rumble?
Let me know in the comments.
And this has been the Wrestling Report.
I hope you're all having a great day; thank you so much for watching Wrestling Hub, and
I'll see you tomorrow with more wrestling news.
For more infomation >> Former Superstar Says He's Returning to WWE, Plans for A.J. Styles | Wrestling Report - Duration: 1:51.-------------------------------------------
Basics: Cleaning out a clogged nozzle! - Duration: 7:32.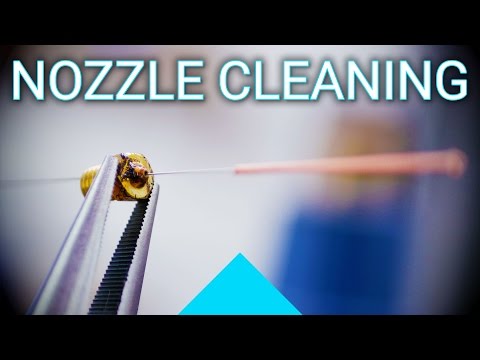
We've all been there: A hotend that just doesn't seem to let any filament through.
While there are a few different things that could cause your printer to behave that way,
a clogged nozzle is a likely cause and one that you take care off easily.
So today i'll walk you through how to identify a blocked nozzle and how you can easily fix
it, often even without taking your 3D printer apart at all.
AprintaPro reached out to me for this sponsored videos series to be featured on their PrintaGuide
platform.
Launching in January, it'll be home to 3D printing tips, tricks and guides.
Check out AprintaPro and the PrintaGuide site at the links in the video description below!
A clogged or partially blocked nozzle is usually fairly easy to make out: If your extruder
motor is struggling to push material through the hotend or you're getting prints that
are mostly air with only very little material making its way down, then it's a good idea
to check the nozzle.
While disengaging your extruder form the filament by pushing the idler lever back, try and push
filament through the heated hotend by hand.
You might get an initial amount of material making it through, but you'll find that
it's either impossible to push or that the extruded material curls heavily right after
leaving the nozzle or extrudes much thinner than what you might be used to.
This can indicate a small particle stuck in the nozzle bore, which we'll need to get
out.
Somehow.
One of the easiest, but also least reliable ways is to grab a wire or an acupuncture or
hypodermic needle that is small enough to fit up the nozzle and try and get the blockage
unstuck.
Obviously, you'll need a needle or wire that is small enough to fit your nozzle bore,
typically 0.4mm, and while some users recommend using a drill bit instead, i'd actually
say not to use one, since they are expensive, break more easily than a solid needle, and
worst of all, can permanently damage the nozzle if you're not super careful.
So as a first try, preheat the nozzle to your regular printing temperature and get cracking
with that needle.
Still being careful not to burn yourself, your goal is not to extract the blockage,
but only to break it up enough so that it slips through the nozzle the next time you
push filament through.
You might have to go through the cycle a few times of fiddling with the needle and pushing
through a bit of filament by hand to check if you've broken up the blockage enough.
Another way that I personally prefer over pushing needles up the hotend, is to use a
cold pull - Ultimaker calls this the "Atomic method", which is similar in concept.
A cold pull works best with slippery, soft materials - so, Nylons, like Taulman's Bridge
filament.
Again, heat up your hotend to the working temperature of your Nylon or Polyamide filament,
push it through the hotend as far as possible, ideally, until your previous material is cleaned
out, which obviously is going to be somewhat hard if your nozzle is, like, completely stuffed,
and then have the hotend cool down.
Now, what i like to do after that is to set the hotend to 110, 120°C and just keep on
pulling on the filament while the hotend is heating until the filament plops out in one
piece.
This should leave you with a perfect negative shape of your hotend's and nozzle's bores
and you will be able to see the contaminant on the end of the filament.
Then cut off the contaminated end, fully heat the hotend again and repeat the process until
the pulled end of your filament comes out clean and you've restored good flow through
the nozzle.
Usually, two or three passes should be enough.
Now, what Ultimaker recommends is actually setting the hotend to a fixed temperature,
90° for PLA, 110° for ABS, waiting until the hotend is at temperature and then yanking
the filament out.
This works fine for Ultimakers, but the keep in mind that both ABS and PLA aren't flexible
enough to be pulled out cold from many other hotend geometries, including the common E3D
v6 setup.
Nylon works fine for this.
Now, if both of these methods don't get your nozzle unclogged, you can always go a
step further and clean the nozzle outside of the printer.
Click up here to learn how to remove your hotend's nozzle safely, but if you've
got the option to, do a cold pull first to empty out as much material from the nozzle
as possible.
With the nozzle removed, you have the choice of either removing the gunk mechanically or
by using solvents.
For mechanical cleanup, it's the same idea as with the nozzle installed - heat it up,
e.g. with a hot air gun set to low, and then carefully scrape out as much of the contaminant
as possible using needles or other pointy tools.
When using hardened nozzles, be very careful not to overheat those, as they will lose their
hardening if you do.
What also works for many materials is simply burning out the nozzle with a blowtorch.
However, if you're unlucky, you might end up with a nozzle that is completely FUBAR,
so i'm not going to recommend this.
But if you're using ABS or PLA, you can actually chemically dissolve most of the plastic
remainder in the nozzle.
For ABS, acetone or more aggressive solvents work well, and PLA somewhat dissolves in ethyl
acetate.
So leave the nozzle in those for a few hours and you should be able to much more easily
clean out out the bore.
If you can, go for a squeaky-clean look with the bore completely freed up.
Now, if these methods didn't get your extruder working perfectly again, you should also check
the teflon liner inside the hotend if your printer has one, and give the extruder a good
staredown to see if it's grinding through filament because the hobbed gear is clogged
up, dull or from the filament being kinked and crooked inside the extruder.
So now that you're left with a functional hotend, how do you prevent it from clogging
up again?
My printers have been running blockage-free for many years now, and it's just a few
simple things: First off, use decent filament.
There've been reports of steel balls contained within dirt cheap filament, and those, of
course, are guaranteed to completely block a nozzle in a heartbeat.
Also, better filament is usually made in a cleaner environment, which means it's only
going to contain components that will actually melt in your printer's hotend.
The same goes for your 3D printer's environment: Keep it clean and dust-free.
If your printer sucks in dust or other particles, those can accumulate and easily clog the nozzle
over time.
If you're uncertain about whether your workspace is clean enough, you can simply use a bit
of foam with a hole punched through to wipe off any dust before it enters the printer
- you'll be surprised how much that actually catches over time!
And lastly, don't cook your filament inside the nozzle.
If you leave the hotend heated up for an extended period of time, chances are the filament is
going to slowly decompose into an unextrudable mess.
So simply turn off the hotend when the printer is idle.
Some machines actually do this on their own.
Alright, so i hope this video is helpful to you.
If you liked it, give it a thumbs up, consider subscribing to the channel, and because Youtube
is being sorta weird about it, remember to also click that bell next to the subscribe
button or you might end up missing some videos altogether.
Also check out the affiliate links from the video description to shop on Amazon, eBay,
Matterhackers and iGo3D, those don't cost you a single penny extra, or if you want to
support this channel with a spare dollar or two, head over to Patreon and get access to
monthly Q&A hangouts and more.
And that's it for today, thanks for watching, and I'll see you in the next one.
-------------------------------------------
The BONES Cast & Producers Reveal Their Favorite Episode | Season 12 | BONES - Duration: 1:54.
HOST: What's your
Thinking back now.
This is last season.
Let's just go down the line here.
Do you have one that just comes to mind fast?
I mean, I really like the circus episode.
You will be amazed.
It's hard to choose one, but I'll
say that that was really fun.
Hey!
[cheering]
Come, Boris.
HOST: David. EMILY DESCHANEL: Go.
Your turn. Go.
This is going to be long, so you might
as well go get a cup of coffee. - No, one episode.
- One episode? - One episode.
Go. - OK, I like the 200th episode.
I'll ballpark it.
EMILY DESCHANEL: Oh, that's awesome.
DAVID BOREANAZ: Love that one.
SEELEY BOOTH: See?
This is why I like to drive.
HOST: All right.
Next.
Go.
HOST: TJ.
Mm-- it's really hard.
Buried car.
EMILY DESCHANEL: Yeah, that's one of my favorites.
Buried car. TJ THYNE: Buried car, yeah.
EMILY DESCHANEL: Oh. OK.
HOST: Michaela.
MICHAELA CONLIN: OK.
The Christmas episode from the first season.
EMILY DESCHANEL: Aw.
TJ THYNE: Oh, yeah, that was [inaudible].
Mine's a little more grim.
The Norwegian death metal episode.
Skalle.
Skalle.
Skalle.
Skalle.
On a pony.
You ever ride a horse, Angela?
ANGELA MONTENEGRO: Uh-- yeah, a couple times.
JAMES AUBREY: Beautiful thing, isn't it?
SEELEY BOOTH: Come on, you're just looking for an excuse
to ride there, pony boy. - Yeah.
Well, I figured while I'm here.
[laughter]
I'd have to say for me it's the pilot.
It's one of the best pilots I've ever seen.
I wouldn't be here if it wasn't for that.
I have to admit, that's pretty cool.
For me it hasn't aired yet.
Whoa.
MICHAEL PETERSON: So we'll make it the finale.
We're going to make that the best episode ever,
so I'm just looking forward to the future here.
[music playing]
-------------------------------------------
YTPH - Harry va espirulai a su primer día de colegio - Duration: 4:08.
-------------------------------------------
QUEEN LATIFAH'S Car Stolen in Gas Station Robbery | TMZ Live - Duration: 3:12.
SO QUEEN LATIFAH, WOW, THIS IS
QUITE THE STORY.
SHE HAS A CAR THAT SHE TOOLED
AROUND IN IN ATLANTA.
KELLY: A MERCEDES, A NICE CAR.
HARVEY: A SECURITY GUARD IS
DRIVING AROUND IN IT A COUPLE OF
DAYS AGO AND GOES TO A GAS
STATION.
AS HE IS GASSING UP, THIS B.M.W.
PULLS UP AND APPARENTLY ONE OF
THE GUYS IN THE B.M.W. JUMPS OUT
OF THE CAR, JUMPS IN THE
MERCEDES AND STARTS THE ENGINE
AND THEN JUST TAKES OFF, BOOKS
IT.
I GUESS THE NOZZLE FLIES OUT AND
THE COPS PUT AN A.P.B. OUT AND
THEY SOMEHOW END UP AT THIS
APARTMENT COMPLEX IN ATLANTA AND
THEY FIND THE CAR, BUT WE FOUND
OUT THAT QUEEN LATIFAH WAS SUPER
WORRIED ABOUT SOMETHING THAT
THIS WAS IN THE TRUNK.
SHE HAD A TUMI BAG.
AND IN THAT BAG, THERE WAS SOME
KIND A CONTRACT, WE DON'T KNOW
WHAT.
THERE WAS SOME KIND OF A
CONTRACT.
KELLY: SOME KIND OF PAPERWORK
THAT SHE DOESN'T WANT EVERYBODY
IN THE WORLD TO SEE.
SHE WAS REALLY CONCERNED ABOUT
THAT.
THAT IS A PRIVACY MATTER.
YOU CAN REPLACE THE THINGS.
HARVEY: THERE WAS SOMETHING, I
DON'T KNOW WHAT KIND OF A
CONTRACT IT WAS.
SHE WAS SUPER WORRIED THEY WERE
GOING TO GET THE CONTRACT AND
TAKE IT.
THEY DID ROOT AROUND THE BAG,
THE THIEVES ROOTED AROUND THE
BAG, WHATEVER THEY TOOK, THEY
LEFT THE CONTRACT, BUT THE CAR
WAS KIND OF A MESS AND THEY'RE
ON THE HUNT.
>> REALLY INTERESTING THAT THIS
SEEMED TO BE THE ONLY THING THAT
SHE WAS CONCERNED ABOUT, SO MUCH
SO THAT THEY ACTUALLY PUT IT IN
THE POLICE REPORT.
SHE WAS LUCKY THEY FOUND IT.
THEY FOUND THE VEHICLE PRETTY
QUICKLY.
HARVEY: THAT'S WHAT I'M TRYING
TO FIGURE OUT.
HOW DID THEY FIND THE VEHICLE IN
THE APARTMENT SO QUICKLY?
KELLY: THE VEHICLE THAT HAD THE
GAS NOZZLE HANGING OUT OF IT.
THE BREAKAWAY ON A GAS NOZZLE,
IF YOU TAKE OFF --
THE BREAKAWAY IS HALFWAY DOWN
THE THING.
HARVEY: BUT THEY GOT INTO THIS
APARTMENT COMPLEX --
>> I BELIEVE IT WAS A TRACKER
WITH THE MERCEDES VEHICLE OF
SOME SORT.
KELLY: THEY HAVE THE TRACKERS.
HARVEY: THAT'S INTERESTING,
THAT'S HOW THEY DID IT.
SO ANYWAY, THE BAD GUYS ARE ON
THE LOOSE STILL.
THE COPS ARE LOOKING AT
SURVEILLANCE VIDEO AND PROBABLY
GOING TO CATCH THESE GUYS.
THEY THINK THEY'RE IN THE
APARTMENT COMPLEX.
CALLER: VINCE FROM CHICAGO.
THE BIGGEST THING HE SHOULD HAVE
DONE FIRST OF ALL, KEEP THE KEY
WITH HIM SO THEY AREN'T ABLE TO
TAKE OFF WITH THE CAR.
IN A MERCEDES EMG LIKE THAT, YOU
HAVE TO TURN THE KEY IN TO START
THE VEHICLE.
AND SECONDLY, KNOW THAT QUEEN
LATIFAH HAD SOMETHING HAPPEN A
BUNCH OF YEARS AGO WITH ANOTHER
DRIVER THAT MAYBE SHE HAS TOLD
THEM TO LEAVE THE KEY IN THE
CAR.
THAT COULD HAVE BEEN ONE OF THE
REASONS WHY HE LEFT THE KEY IN
THE CAR AS WELL, THEY HAD A
DRIVER A BUNCH OF YEARS AGO GET
HURT THAT WAS DRIVING FOR HER AS
WELL OR A DIFFERENT CAR.
HARVEY: I GOT TO CHANGE SOME
HABITS.
I HAVE BEEN THINKING ABOUT THIS.
A LOT OF HABITS I GOT TO CHANGE.
KELLY: ESPECIALLY WHEN YOU'VE
GOT THE PUSH BUTTON THING, I
LEAVE THEM IN THE CAR.
HARVEY: IF YOU TOOK THE KEY OUT
OF THE CAR, IT'S CLOSE ENOUGH TO
THE CAR THAT IT WOULD START.
KELLY: IT WOULD START, BUT
EVENTUALLY IT WOULD STOP.
HARVEY: DOES IT JUST STOP?
KELLY: YEAH.
I HAVE DONE IT BEFORE WHERE I
HAVE STARTED IT AND THE KEYS ARE
AT YOUR HOUSE AND LOOK AT ME.
HALFWAY DOWN THE ROAD, NOPE.
HARVEY: IT JUST STOPS.
KELLY: A WARNING AND IT JUST
STOPS.
-------------------------------------------
Throw Your O | Best of 2016 - Duration: 1:26.
-------------------------------------------
China Opens World's Highest Bridge - Duration: 1:01.
-------------------------------------------
Person shot on Dandy Court in Virginia Beach - Duration: 0:35.
RIGHT OFF THE TOP AT 6--
TWO BREAKING STORIES.
FIRST-- THIS VIDEO JUST
IN FROM VIRGINIA BEACH.
A SHOOTING ON DANDY COURT
AROUND 4-15 THIS
AFTERNOON.
THAT'S JUST OFF NORTH
WITCHDUCK ROAD. WE'RE
TOLD THE MALE VICTIM
SUFFERED NON-
LIFE THREATENING
INJURIES. HOWEVER--
THERE'S STILL A VERY
ACTIVE
SCENE OUT THERE FOR
NEARLY TWO HOURS. LIZ
KILMER IS THERE.
LOOK FOR MORE AT 7 ON FOX
43-- AND TONIGHT AT 10
AND 11.
-------------------------------------------
Video: Payments in class action lawsuit in Levy case revealed - Duration: 1:45.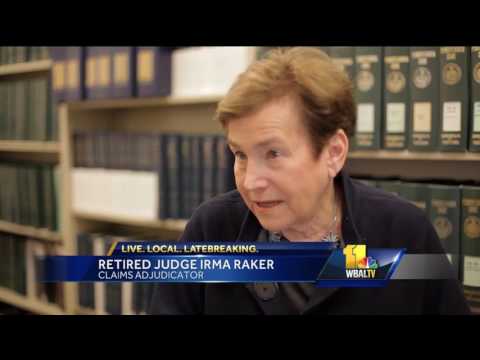
MORE THAN TWO YEARS AFTER A
JUDGE APPROVED
$190 MILLION SETTLEMENT BETWEEN
JOHNS HOPKINS HOSPITAL AND
PATIENTS OF DR. NIKITA LEVY, 11
NEWS HAS LEARNED THE NEXT PHASE
IN THE PROCESS IS UNDERWAY
DETERMINATION LETTERS SENT TO
THE MEMBERS OF THE LEVY
SETTLEMENT CLASS INFORMING EACH
PLAINTIFF HOW MUCH SHE'S BEEN
AWARDED.
THERE ARE 9,600 WOMEN IN THIS
CLASS ACTION CASE.
JUDGE RAKER: WE UNDERSTAND THAT
EVERYONE WOULD LIKE THEIR MONE
AS SOON AS POSSIBLE, AND WE ARE
TRYING TO ACCOMMODATE THAT
KATE: ON THE WEBSITE CREATED TO
KEEP THE CLASS MEMBERS
UP-TO-DATE, THE CLAI
ADJUDICATOR, RETIRED JUDGE IRMA
RAKER, POSTED A VIDEO EXPLAINING
THE PROCESS AND URGING PATIENCE.
JUDGE RAKER: YOU HAVE
REMEMBER, THERE ARE 9,600 WOMEN
IN THIS CLASS ACTION.
IT'S PROBABLY ONE OF THE
BIGGEST, OR THE BIGGEST, CLA
ACTION CASE OF ITS TYPE IN THE
COUNTRY.
KATE: SETTLEMENT ADMINISTRATORS
AND THE CHAIRMAN OF THE
PLAINTIFFS' STEERING COMMITTEE
FOR THIS CLASS ACTION DID NO
RETURN OUR CALLS AND EMAILS
TODAY TO CONFIRM THE AMOUN
AWARDED, BUT ADMINISTRATORS HAD
PREVIOUSLY SAID THE PLAINTIF
WOULD BE DIVIDED INTO FOUR
CATEGORIES BASED ON SEVERITY OF
INJURIES
DOCUMENTS OBTAINED BY 11 NEWS,
REPORTEDLY SENT TO PLAINTIFFS,
OUTLINE THE PAYMENT ALLOCATIONS
FOR MEMBERS OF FOUR GROUPS.
THE AMOUNTS LISTED IN THOSE
DOCUMENTS RANGE FROM ABOUT $18
TO MORE THAN $26,000
STAN REGARDLESS OF THE FINAL
-------------------------------------------
Meet Lauren Marie, Certified Facilitator of Access Consciousness - Duration: 4:48.
Hey everyone! Simone Milasas and this is
Lauren Marie and we're doing a little
feature of meet the Access Consciousness
Facilitator. So I've got five quick
questions for your Lauren ok? Ready when
So number one how did you find Access
Consciousness? I used to be an
Acupuncturist and I had a client of mine
who started doing Access and she came in
to see me, we would do sessions every
week or so and she would come in a
little bit with change and she leave and
she would come back and one day she came in and
she was so completely different and
everything in her life that we've been
working on for two years was like
totally changed and I was like okay wait,
what are you doing and she was like oh
my god you have to try this it's so cool
it's called access. I had been doing
Acupuncture my patients are looking for
more and asking for more and searching
for something that could take these
tools that I had further. So I just
signed up for my Bars Class like the next
weekend.
Nice. Okay question 2 - So what made
you choose to become a Certified
Facilitator. I just knew I had to be
it. I had to be there, I had to do it. I went
as fast as I could, I think it was less
than a year from my first class to
becoming a Facilitator. I just knew I had
to! Number three - what is your go-to too?l
I can only pick one?
Yes for now what's your go-to tool? Right
now?
Right now it's using the clearing
statement, is that too no basic?
So what is the Clearing Statement?
It's right and wrong, good and bad, pod and poc all
nines, shorts, boys and beyonds and I've
just been using it a lot because we have
Christmas time and we have in-laws and
everything that's coming up around all
of that I've just been "everything
that is pod and poc, pod and poc"
and I've just been running the clearing
statement a tonne. So the pod and poc is
you can just shorten it and even if you
don't know what we're talking about that
you can say all that crazy stuff that
they said on the video or you can go and
check out theclearingstatement.com
with our friend Dr. Dain
talking about it. Number four - what
would you like to see change in the
world? Iif everyone could have a little
bit of what my two babies have which is
this like curiosity and joy and enthusiasm
for living. If every person on the planet
had even like 1% of that -
sounds like my dog -
yes, the joy - the dogs and
children. So every other the being on the
planet
So everyone to
be a child in or a dog...
yeah oh my god yeah alright yeah! Number
five
what is the greatest change you have had
or witnessed in a client using the Access
Consciousness tools and techniques? There
was a guy who came to me years ago when
I first started doing...
I was an acupuncture is doing
Access with my patients and acupuncture.
But there's a guy that called me and he
had like panic attacks and he couldn't
leave the house, it had been years since
he had left his house and he had to be
driven places if you would leave and it
was very severe panic attacks and I just
knew when he called I was like okay
you're calling for acupuncture but I
just learned this other stuff like it's
a little bit weird do you mind if I do
this?
He's like I don't care if you put a
monkey on my head, it doesn't
matter like if it's gonna work
So I ran his bars
and I ran some clearings with him and he
walked out and I didn't hear from him
ever again,
well until I called him three weeks
later. I was like whatever happened to that guy and
he goes oh my goodness never called you
because I've been like back to work and
I've left my house and i'm like driving
like the only thing I haven't tried yet
is flying butIi've been using that like
thing that you've taught me to clear
stuff and he completely
changed his life like he had gone back
to living and it just
gives me chills
and he had been in therapy for 10
years, three times a week and on
medication and
nothing was touching that and it was like one
session. So that was pretty dramatic.
Wow that's cool, how does it get any better than that?
Lauren, what classes do you facilitate at the
moment? I do Bars classes and the
Foundation classes and Joy of Business
classes, Being You Adventure
classes. Where can people find you
meetlaurenmarie.com and accessonsciousness.com
and search Lauren Marie. You live in
Queensland at the moment in
Australia.
I will travel.
Alright, so this is Meet Your Certified
Facilitator in Australia! First one up
- Lauren Marie.
Thanks for joining us and we'll see you
next time, bye!
-------------------------------------------
Top Local Stories That Made Headlines In 2016 - Pt. 2 - Duration: 6:07.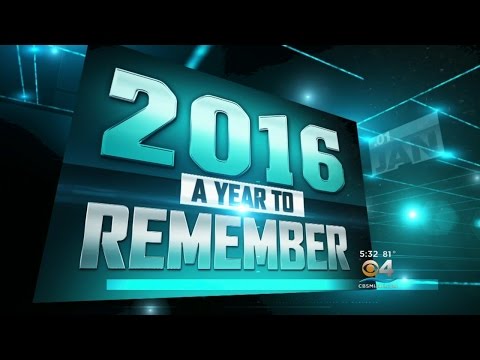
ALL OF THE
INMATES WILL FACE NEW CHARGES
FOR MAKING THE ESCAPE.
2016, A YEAR TO REMEMBER.
TONIGHT WE COMPLETE OUR
COUNTDOWN OF THE TOP 10 LOCAL
STORIES FOR THE PAST 12 MONTHS.
EVERY ONE ALSO BECAME A BIG
STORY ACROSS THE NATION AND
WORLD.
HERE'S CBS 4'S DAVID
SUTTA.
Reporter: AS WE LOOK BACK ON
2016 THERE ARE STORIES YOU WILL
NEVER FORGET INCLUDING THAT ONE
THAT DIDN'T REALLY HAPPEN.
IT
WAS EARLY OCTOBER AND A MONSTER
STORM WAS BUILDING IN THE
CARIBBEAN.
HAITI AND THE
BAHAMAS TOOK A BEATING.
THE
POTENTIAL CATEGORY 4 HURRICANE
WAS HEADED FOR FLORIDA.
ON TOP OF THE WINDS THE STORM
SURGES ARE GOING TO BE
SIGNIFICANT.
Reporter: WITH MUCH OF THE
STATE OF FLORIDA IN THE CONE
STORE SHELVES WERE WIPED CLEAN,
GAS STATIONS ON EMPTY.
A PANIC
SET IN FOR MANY AS WE PREPARED
FOR THE WORST AND THEN NOT A
LOT
HAPPENED.
MATTHEW SCOOTED UP
THE COASTLINE.
IT'S MORE
POWERFUL WINDS KEPT OFFSHORE.
IT'S WORTH NOTING FLORIDA HAD
GONE 10 YEARS WITHOUT A STORM
PRIOR TO 2016.
NUMBER 4 ON OUR
LIST, A TRAGEDY THAT TOOK PLACE
JUST OFF OF SOUTH BEACH,
SEPTEMBER 25TH AROUND 3:00 A.M.
THE CALLS WENT OUT OF A BOAT
CRASHING IN THE GOVERNMENT CUT
JETTY.
OUR BOAT RESPONDED AND FOUND
A
BOAT ON THE SIDE OF THE
JETTIES.
THEY FOUND THREE VICTIMS.
Reporter: THE VICTIMS ALL
YOUNG MEN INCLUDED MIAMI
MARLINS
SUPER STAR HOE HEY FERNANDEZ.
HE WAS A GREAT -- JOSE
FERNANDEZ.
HE WAS A GREAT KID,
DISCIPLINED.
Reporter: HIS DEATH SHOCKED
MANY IN THE COMMUNITY.
I'D PREFER NOT TO THINK OF
THIS TRAGEDY AS THE END OF HIS
LIFE, BUT RATHER THE BEGINNING
OF HIS LEGEND, HIS MEMORY, AND
HIS LOVE THAT WILL ENDURE
FOREVER.
Reporter: IN THE DAYS AND
WEEKS THAT FOLLOWED WE LEARNED
HE HAD BEEN DRINKING IN
BRICKELL
THAT NIGHT.
ALCOHOL AS OF RIGHT NOW WAS
NOT INVOLVED OR NO OTHER
ILLEGAL
DRUGS WERE FOUND ON THE VESSEL.
Reporter: DESPITE INITIAL
REPORTS HIS AUTOPSY CONFIRMED
FERNANDEZ WAS INTOXICATED AND
HAD COCAINE IN HIS SYSTEM AT
THE
TIME OF THE FATAL CRASH.
NUMBER
3 WAS A PEST TO SAY THE LEAST.
THIS HIP AND COLORFUL MIAMI
NEIGHBORHOOD IS GROUND ZERO FOR
ZIKA.
Reporter: 2016 ROB WINWOOD
WENT INTO A WORLD SPOTLIGHT AS
ZIKA LANDED IN THE INSTITUTIONS
WE'RE BEING VERY AGGRESSIVE AT
TESTING -- LANDED IN THES
UNITED
STATES.
WE'RE BEING VERY AGGRESSIVE
--
LANDED IN THE UNITED STATES.
WE'RE BEING VERY AGGRESSIVE.
I DON'T WANT TO GO HOME.
I
DON'T WANT TO BE IN THIS AREA
ANYMORE.
Reporter: THE CDC ADVISED
PREGNANT WOMAN TO AVOID AREA.
A
SHORT TIME LATER -- TO AVOID
THE
AREA.
THE MOSQUITOES TARGETED
THE LIFEBLOOD OF THE ISLAND,
SOUTH BEACH.
IT WILL HAVE AN EFFECT ON THE
ECONOMY.
Reporter: AFTER MONTHS OF
SPRAYING, COVERING UP, AND
CLEANING UP, THIS MONTH THE
GOVERNOR DECLARED VICTORY.
THE SOUTH BEACH AREA DOES NOT
HAVE ANY LOCAL TRANSMISSION OF
ZIKA AND THAT'S A VERY GOOD DAY
FOR OUR STATE.
Reporter: NUMBER 2 ON OUR
LIST IS THE DEADLIEST SHOOTING
IN U.S. HISTORY THE PULSE
NIGHTCLUB SHOOTING IN ORLANDO,
FLORIDA.
911 TAPES RELEASED
THIS YEAR ILLUSTRATE THE TERROR
THAT HAPPENED ON JUNE 12TH.
CLUB GOERS ON THE PHONE WITH
911
PLEADING FOR HELP AS THE
GUNMAN,
OMAR MATIN SYSTEMATICALLY WENT
THROUGH THE CLUB SHOOTING
PEOPLE.
HE CALLED 911 HIMSELF
TO MICK HIS CASE FOR THE DEADLY
RAMPAGE.
CAN YOU TELL ME WHERE YOU ARE
RIGHT NOW SO I CAN GET YOU SOME
HELP?
NO, BECAUSE YOU HAVE TO TELL
AMERICA TO STOP BOMBING SYRIA
AND IRAQ.
THEY'RE KILLING A LOT
OF INNOCENT PEOPLE, SO WHAT AM
I
TO DO HERE WHEN MY PEOPLE ARE
GETTING KILLED OVER THERE.
DO
YOU GET WHAT I'M SAYING?
Reporter: BY THE TIME
AUTHORITIES STORMED THE
BUILDING
AND KILLED HIM, HE HAD KILLED
49
PEOPLE AND INJURED 53 OTHERS.
THE NUMBER 1 STORY OF 2016 IS
ONE THAT SOUTH FLORIDA HAD BEEN
ANTICIPATING FOR THE GREATER
PART OF TWO DECADES, THE DEATH
OF FIDEL CASTRO.
CUBA'S FORMER
PRESIDENT SHAPED FAR MORE THAN
CUBA'S LANDSCAPE OVER HIS
LIFETIME.
HE PUT THE UNITED
STATES ON ALERT DURING THE
CUBAN
MISSILE CRISIS, DEFEATED A
U.S.-BACKED MILITIA, DIVIDE AN
ECONOMIC EMBARGO AND CREATED AN
ENTIRE COMMUNITY IN MIAMI OF
COMPILES.
MIAMI'S CUBAN
EXILES -- EXILES.
MIAMI'S CUBAN
EXILES TOOK TO THE STREET TO
CELEBRATE HIS DEATH.
THE CUBAN SENTENCES AND CUBA
CELEBRATE.
Reporter: IN CUBA THE MOOD
WAS QUITE DIFFERENT.
MY DAUGHTER HAS BENEFITED SO
MUCH FROM HIS WORK.
Reporter: CUBA HONORED HIS
LIFE WITH NINE DAYS OF MOURNING
[ SPEAKING IN SPANISH ]
Reporter: HIS BROTHER STILL
HOLDS POWER OVER THE COUNTRY.
QUESTIONS REMAIN OVER WHAT WILL
HAPPEN IN 2017.
[CHEERING]
Reporter: 2016 WAS IF YOU
FEEL TRAGEDIES, TRIUMPHS, AND A
FEW SURPRISES.
WE LIFT POLITICS
OUT OF OUR TOP LOCAL STORIES,
BUT WE WOULD BE REMISS IF WE
DIDN'T AT LEAST ACKNOWLEDGE
2016
WAS BY FAR AN HISTORIC HERE FOR
DONALD TRUMP AND REPUBLICANS.
--
HISTORIC YEAR FOR DONALD TRUMP
AND REPUBLICANS.
THAT WAS DAVID SUTTER
REPORTING.
WE WITNESSED HISTORY AND NOW
-------------------------------------------
Can You Die From A Broken Heart? - Duration: 2:33.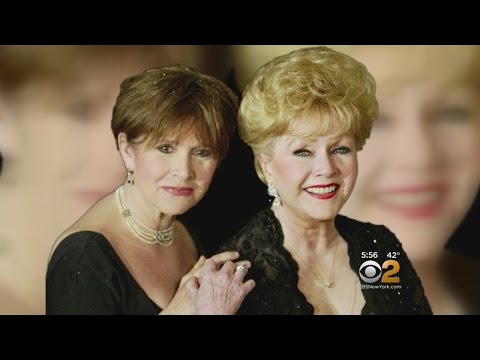
THE WORLD IS STILL REELING
OVER THE SUDDEN DEATHS OF
CARRIE FISHER AND HER MOTHER,
DEBBIE REYNOLDS, JUST ONE DAY
LATER.
MANY PEOPLE ARE WONDERING IN
THE SHOCK OF LOSING HER
DAUGHTER COULD HAVE TRIGGERED
HER STROKE.
CBS 2'S DR. MAX GOMEZ SAYS
THERE REALLY IS SUCH A THING AS
DYING OF A BROKEN HEART?
THERE REALLY IS ACTUALLY.
YOU KNOW, DYING OF A BROKEN
HEART HAS BEEN THE STUFF OF
POETRY AND LOVE STORIES
FOREVER.
TURNS OUT A SEVERE EMOTIONAL
SHOCK CAN ACTUALLY TRIGGER
WHAT'S BECOME KNOWN AS BROKEN
HEART SYNDROME.
DEBBIE REYNOLDS REPORTEDLY
SUFFERED A STROKE WHICH CAN
LOOK SIMILAR TO THE UNTRAINED
EYE.
SHE WAS AMERICA'S SWEETHEART
DANCING HER WAY INTO OUR
HEARTS.
BUT COULD IT HAVE BEEN A BROKEN
HEART THAT FELL THE UNSINKABLE
MOLLY BROWN?
YOU CAN DIE OF A BROKEN
HEART.
Reporter: THIS DOCTOR HAS
STUDIED SOMETHING CALLED [ NON-
ENGLISH LANGUAGE ]
CARDIOMYOPATHY.
MEDICAL LANGUAGE FOR BROKEN
HEART SYNDROME.
SHE SAYS IT IS MEDICALLY
CONCEIVABLE THAT THE SUDDEN
DEATH OF HER DAUGHTER CARRIE
FISHER COULD HAVE CAUSED
REYNOLDS' DEATH.
WE THINK OF BROKEN HEART
SYNDROME IT MAY BE A REAL SURGE
ADRENALINE THAT'S TOXIC TO THE
HEART MUSCLE OR IN THE ARTERIES
GOING INTO SPASM.
THE HEART MUSCLE IN LARGE PART
DOESN'T MOVE AS WELL AS IT'S
SUPPOSED TO AND IT FEELS LIKE A
HEART ATTACK, LOOKS LIKE ONE TO
THE DOCTORS AND IT IS A FORM OF
HEART ATTACK.
Reporter: HIS SON SAID HIS
MOTHER HAD A STROKE.
WE DON'T KNOW THE EXACT CAUSE
OF DEATH BUT DR. REYNOLDS SAYS
A LAYPERSON CAN MISTAKE A HEART
ATTACK FOR A STROKE OR SEVERE
EMOTIONAL STRONG COULD LEAD TO
A STROKE IN WAYS NOT RELATED TO
BROKEN HEART SYNDROME.
WE WOULD EXPECT THAT A
SEVERE EMOTIONAL STRESS WOULD
RAISE THE BLOOD PRESSURE VERY
HIGH THAT COULD CAUSE A PROBLEM
WITH THE BRAIN AND LEAD TO A
STROKE DIRECTLY OR IT COULD
CAUSE HEART STRAIN AND LEAD TO
HEART ATTACK BECAUSE OF THE
VERY HIGH BLOOD PRESSURE.
Reporter: WHILE THERE'S NO
WAY TO AVOID THE BLOWS THAT ARE
OFTEN PART OF LIFE, DR.
REYNOLDS SAYS THAT CONTROLLING
OUR CARDIOVASCULAR RISK
FACTORS, STRESS, BLOOD
PRESSURE, BLOOD SUGAR,
CHOLESTEROL, WEIGHT AND
SMOKING, MAY GIVE US ENOUGH
RESILIENCE TO SURVIVE SEVERE
EMOTIONAL SHOCKS.
AND WOMEN OFTEN SUFFER
DIFFERENT HEART ATTACK SYMPTOMS
THAN MEN.
THEY DON'T NECESSARILY HAVE
THAT CRUSHING CHEST PAIN T CAN
BE SUBTLE, BACK, NECK, JAW, OR
EVEN TOOTH PAIN.
OR WHAT FEELS LIKE INDIGESTION,
NAUSEA AND SWEATING.
THE LESSON HERE IS IF YOU DON'T
FEEL RIGHT GET TO THE HOSPITAL.
A LOT OF PEOPLE ESPECIALLY THIS
TIME OF YEAR THEY DON'T WANT TO
BOTHER PEOPLE THAT SORT OF
THING -- GET TO THE HOSPITAL.
DO YOU NECESSARILY HAVE TO
HAVE ANOTHER CONDITION TO CAUSE
THIS TO HAPPEN?
-------------------------------------------
Burger King, Tim Hortons to Serve Antibiotic-Free Chicken - Duration: 0:54.
-------------------------------------------
Video: Suspect in deputy shooting had domestic violence history - Duration: 2:20.
SED OF DOMESTIC VIOLENCE IN
1997 AND LAST YEAR.
IN CHESTERTOWN ON EDMORE ROAD,
THE FAMILY OF JAMES RICH
DECLINED COMMENT.
MARYLAND STATE POLICE NOW
HANDLING THE INVESTIGATION OF
THE POLICE-INVOLVED SHOOTING
THAT KILLED THE 52-YEAR-OLD AND
WOUNDED QUEEN ANNE'S COUNTY
SHERIFF'S DEPUTY WARREN HOGAN.
>> WELL I SEEN EVERYTHING GOING
HAYWIRE OUT HERE.
>> WHEN WE HEARD THOSE GUNSHOTS,
THAT SCARED US BECAUSE IT WAS
CLOSE, YOU COULD TELL THAT.
BARRY: JEAN AND JOHN EDWARDS
LIVE NEXT DOOR.
THEY SAY THE SOUNDS OF GUN SHOTS
WOKE THEM UP.
>> ABOUT 7:00 OR 8:00, I'M SURE
IT WAS PROBABLY LIKE THAT, AND
HE RAN OVER THERE.
WE COULD HER HIM SCREAMING AND
HOLLERING, THE SON.
BARRY: THE EDWARDS CALLED
THE YOUNG MAN'S FATHER A GOOD
NEIGHBOR. THEY'VE KNOWN HIM FOR
17 YEARS.
>> WE JUST MERELY SPOKE.
IF WE HAD A PROBLEM, HE WAS
THERE FOR US.
BARRY: INVESTIGATORS SAY THIS
ALL STARTED WITH A DOMESTIC
DISPUTE BETWEEN RICH AND HIS
GIRLFRIEND.
COURT DOCUMENTS SHOW HE AND HIS
WIFE IN THE PROCESS OF GETTING A
DIVORCE.
IN 2015, ELIZABETH RICH SOUGHT
AND RECEIVED A PROTECTIVE ORDER
AFTER CLAIMING IN A PETITION
"MY HUSBAND MAKES THREATS THAT
HE WILL KNOCK MY GLASSES OFF MY
FACE.
HE TELLS ME IF I TAKE HIS SON I
WILL BE A DEAD MOTHER.
THE MARRIAGE HAS BEEN ABUSIVE
PHYSICALLY, MENTALLY AND
EMOTIONALLY FOR YEARS."
THOSE YEARS ARE LISTED FROM 1997
TO 2015.
ALSO HE "HAS ACCESS TO THE
FOLLOWING ITEMS: 10 SHOTGUNS, 1
BOW, 2 HANDGUNS."
THOSE GUNS REMOVED FROM THE
HOME, CONFISCATED BY QUEEN
ANNE'S COUNTY SHERIFF'S
DEPUTIES.
RICH GOT HIS LONG GUNS BACK.
THE SHERIFF'S OFFICE SAYING HE
REACHED ELIGIBILITY WHEN THE
PROTECTIVE ORDER ENDED IN JULY
OF THIS YEAR.
THE TWO HANDGUNS STILL IN THE
CUSTODY OF THE SHERIFF.
>> TO ME IT DIDN'T SOUND LIKE
HIM.
DO YOU KNOW WHAT I AM SAYING?
HE WAS ALWAYS LIKE A QUIET
SPOKEN MAN.
HE WORKED EVERYDAY AND HE WAS
JUST QUIET.
BARRY: ONCE MARYLAND STATE
POLICE COMPLETE THEIR
INVESTIGATION, THEIR FINDINGS
WILL THEN GO TO THE QUEEN ANNE'S
-------------------------------------------
Middle School Implements Random Drug Testing - Duration: 2:04.
HARD BY THE OPIOD EPIDEMIC.
CBS 2'S MEG BAKER HAS THE STORY
NEW AT 5:30.
Reporter: OUTSIDE LAZY
TOWNSHIP MIDDLE SCHOOL ARE TWO
BILLBOARDS SIGNED BY STUDENTS.
WE PLEDGE TO STAY DRUG-FREE.
THE DISTRICT IS TAKING AN EXTRA
STEP TO ENSURE THAT WITH RANDOM
DRUG TESTING FOR 7th AND 8th
GRADERS WHEN EXPERIMENTATION
OFTEN STARTS.
THERE'S BEEN MIXED FEELINGS
OUT THERE COMMENTARY ABOUT
STUDENT RIGHTS AND OVERSTEPPING
BOUNDARIES BUT WE ARE GIVING
PEOPLE AN OPTION.
I'D RATHER DO SOMETHING THAN
SIT ON MY HANDS AND JUST SAY
WHAT'S NEXT?
WHAT ARE WE GOING TO DO?
Reporter: THE SUPERINTENDENT
SAYS MORE THAN 100 FAMILIES
HAVE SIGNED UP FOR THE PROGRAM
SO FAR KNOWING THAT AS THEIR
CHILD WALKS THROUGH THOSE DOORS
THEY COULD BE TESTED AT ANY
TIME.
IT'S SCARY AT THAT AGE BUT
THE HORROR STORIES THAT I HEAR.
Reporter: THIS MOTHER SAYS
THIS IS AN EXTRA BARRIER TO
PREVENT DRUG USE.
IT SEEMS THAT THE DRUG
PROBLEM STARTING YOUNGER AND
YOUNGER.
SO IT'S FANTASTIC THEY CATCH IT
YOUNG BECAUSE IT'S HAPPENING A
LOT IN THE MIDDLE SCHOOL.
Reporter: CAROLYN HAS FOUR
KIDS IN THE DIRECT AND SIGNED
THEM UP.
UNFORTUNATELY, PEOPLE FEEL
THAT THE STUDENTS WHO SHOULD BE
TESTED, THEIR PARENTS PROBABLY
WON'T SIGN THEM UP TO BE.
Reporter: MORE THAN 180
PEOPLE HAVE DIED FROM OVERDOSES
IN OCEAN COUNTY SO FAR THIS
YEAR.
STATEWIDE, DEATHS ARE UP
SHARPLY TOO.
MAYBE IT'S GOING TO HELP
THIS DRUG PROBLEM WE HAVE IN
OUR TOWN.
Reporter: THE SUPERINTENDENT
SAYS IT SHOULD PSYCHOLOGICALLY
KIDS COMBAT PEER PRESSURE.
IF OFFERED DRUGS THEY CAN SAY
NO, I'M GOING TO BE TESTED.
THE FOR THE CHILDREN TO
SHARE I UNDERSTAND THAT THEY
HAVE A SAFE OUT TO -- TO DENY
EVEN THE EXPERIMENTATION WITH
DRUGS.
Reporter: ITS PROGRAM IS
ADMINISTERED BY A THIRD PARTY
COST ABOUT $10,000 A YEAR.
THE SUPERINTENDENT SAYS IT'S
WORTH IT TO BATTLE THIS
EPIDEMIC TOGETHER N LAZY
TOWNSHIP, NEW JERSEY, MEG
BAKER, CBS 2 NEWS.
THE MIDDLE SCHOOL PROGRAM IS
A NEW EXTENSION OF THE HIGH
SCHOOL'S DRUG TESTING PROGRAM.
-------------------------------------------
Teen Steps Up To Help Woman On Train - Duration: 1:47.
ON A SUBWAY TRAIN IN BROOKLYN.
NEW AT 5:00 CBS 2'S RAEGAN
MEDGIE SPOKE WITH THE TEEN.
Reporter: THIS MAN BEING
ARRESTED MAY NEVER HAVE
HAPPENED IF IT WASN'T FOR 17-
YEAR-OLD AHMED KHALIFA.
SOMETHING EVERYBODY SHOULD
DO.
RANDOM ACT OF KINDNESS.
Reporter: THE MUSLIM TEEN
WAS ON THE Q HEADING HOME TO
THE MIDWOOD SECTION OF BROOKLYN
TUESDAY NIGHT WHEN HE SAW A 56-
YEAR-OLD JEWISH WOMAN GET
ATTACKED OUT OF NOWHERE.
HE SMACKED HER ACROSS THE
FACE.
SHE WAS BLEEDING AND HER
GLASSES WERE ON THE FLOOR.
SHE WAS JUST REALLY SAD.
SHE WAS LIKE WHY WOULD DOE
THIS?
THE ATTACKER IS A 31-YEAR-
OLD MAN NAMED RAVON JONES.
KHALIFA CALLED TO THE
KENTUCKYER.
I WAS TELLING HIM TO STOP,
STOP, CALL THE AMBULANCE OF THE
SHE IS HURT CALLING TO THE
CONDUCTOR AND AFTER THAT HE SAW
WHAT HAPPENED SO I STARTED
RUNNING AND THEN I SAW A GUY HE
WAS LIKE HE WENT THAT WAY.
Reporter: KHALIFA GOT OFF
THE TRAIN AND FOLLOWED JONES
FOR TEN BLOCKS HERE ON FOSTER
AVENUE.
AT ONE POINT, HE LOST THE GUY
AND SOMEONE OFFERED TO HELP.
HE LET ME GET IN THE CAR
WITH HIM AND WE STARTED LOOKING
AND WE FOUND HIM AND HE GOT ON
THE BUS THE B6 8 SO WE FOLLOWED
THE B6 8 THE WHOLE WAY UNTIL
THE POLICE FINALLY CAUGHT UP
WITH US.
Reporter: THEN JONES WAS
ARRESTED.
JUST GOES TO SHOW YOU THE
NEW GENERATION IS WILLING TO
STICK UP FOR THINGS THAT ARE
RIGHT AND DO IT WITHOUT EVEN
THINKING ABOUT IT.
IT'S ALMOST IN THEIR BLOOD.
THAT'S GREAT.
I DON'T KNOW WHY EVERYONE
IS, LIKE, AMAZED.
IT'S NOT THE HERO, LIKE,.
Reporter: HE SAYS JONES WAS
VIOLENT AND SAID NASTY THINGS
TO HIM WHO SAID HE WOULD DO IT
ALL OVER AGAIN BECAUSE IT'S THE
RIGHT THING TO DO.
IN BROOKLYN, RAEGAN MEDGIE, CBS
2 NEWS.
POLICE ARE STILL TRYING TO
FIND OUT WHY THE HOMELESS
-------------------------------------------
Good Riddance To 2016 - Duration: 2:05.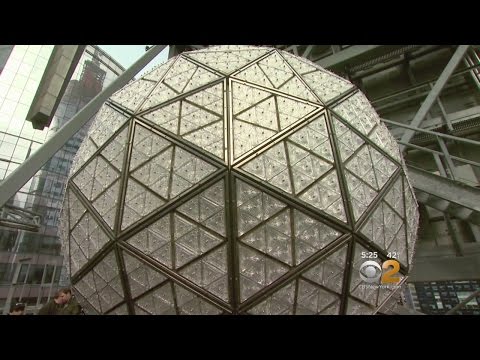
A FAMILY RALLIES FOR A ONE-
YEAR-OLD BOY.
HEAR FROM THE AUNT WHO SAVED
HIS LIFE.
ON SOCIAL MEDIA ON THE
SUBWAY, EVEN ON THE STREET, YOU
HAVE PROBABLY HEARD IT.
SO MANY PEOPLE SAYING 2016 WAS
THE WORST YEAR EVER.
THE QUESTION IS WHY.
WAS IT REALLY THAT BAD?
VALERIE CASTRO FOUND OUT PEOPLE
CAN'T WAIT FOR 2017 TO ARRIVE.
IT WAS LIKE OH, MY GOD LIKE
THIS YEAR TOTALLY JUST BLOWS.
IT'S BEEN A CRAZY YEAR.
IT SUCKED.
Reporter: FOR ONE REASON OR
ANOTHER MANY PEOPLE SEEMED TO
THINK 2016 WAS AN EXCEPTIONALLY
BAD YEAR.
IT WAS TERRIBLE PERSONALLY
AND PUBLICLY.
Reporter: CHALK IT UP TO A
CONTENTIOUS ELECTION THE
CONFLICT IN SYRIA, DEADLY
TERRORIST ATTACKS AND REMEMBER
THE ZIKA VIRUS?
ADD TO THAT THAT THERE HAVE
BEEN THE DEATHS OF A LOT OF
REALLY IMPORTANT PEOPLE IN OUR
LIVES MUSICIANS, ACTORS,
ACTRESSES.
Reporter: PRINCE DEAD AT 57.
FLORENCE HENDERSON DEAD AT 82.
DAVID BOWIE DEAD AT 69.
GEORGE MICHAEL, ARNOLD PALMER,
JOHN GLENN AND ALAN THICKE,
CARRIE FISHER AND HER MOTHER
DEBBIE REYNOLDS.
WHO IS NEXT?
Reporter: SOME HAVE GONE AS
FAR AS TO CURSE THE CURRENT
YEAR WITH T-SHIRTS MUGS AND
BUMPER STICKERS.
A HBO HOST ENDED HIS SHOW LAST
NIGHT WITH A MONTAGE OF SORTS.
BLOWING UP 2016 INTO
SMITHEREENS.
SO IS IT REALLY ALL THAT BAD?
THE END OF THE YEAR REALLY
BROUGHT OUT SO MUCH HATRED AND
DISGUST AND FRUSTRATION IN SO
MANY DIFFERENT AREAS.
PEOPLE ARE REALLY NOT SURE HOW
TO HANDLE IT.
Reporter: SO LET GO.
NEW YEAR'S EVE AND TIMES SQUARE
IS JUST ONE WAY TO SAY GOOD-BYE
TO 2016.
THE EXPERTS SAY FIND A SENDOFF
THAT'S MEANINGFUL TO YOU.
IN TIMES SQUARE WEDNESDAY IT
WAS GOOD RIDDANCE DAY A CHANCE
TO WRITE DOWN ALL THE BAD TO BE
HAULED OFF TO A SHREDDER.
OTHERS SMASHED SYMBOLS OF THEIR
YEAR.
WITH THE BAD OUT OF THE WAY,
FOCUS ON THE GOOD.
I GOT A RAISE.
SO I GUESS LIKE I HAD THAT AND
LIKE I DO HAVE GREAT FRIENDS
AND I DO HAVE LIKE A LOVING
FAMILY.
2017 IS GOING TO BE
SPECTACULAR.
Reporter: AND CHEER UP.
-------------------------------------------
Video: Queen Anne's County Sheriff's deputy injured in shooting - Duration: 1:52.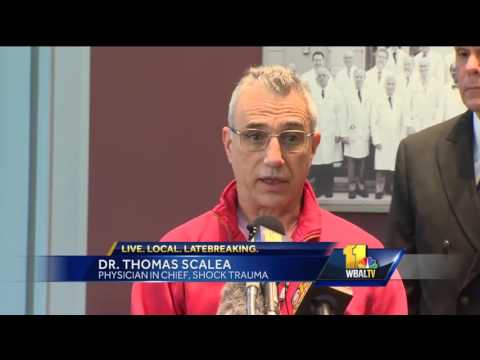
COULD TAKE MANY MORE
SURGERIES, WEEKS, EVEN MONTHS TO
RECOVER.
IT ALL STARTED WITH A TEXT
MESSAGE AROUND 9:30 WEDNESDAY
NIGHT.
>> THE SUSPECT'S GIRLFRIEND, WHO
HAD BEEN STAYING WITH HIM AT HIS
RESIDENCE, SENT A TEXT MESSAGE
TO HER FATHER STATING SHE AND
THE SUSPECT HAD BEEN INVOLVED IN
A PHYSICAL ALTERCATION.
KIM: THE VICTIM'S FATHER PICKED
HER UP AND TOOK HER TO THE QUEEN
NNE'S COUNTY SHERIFF'S OFFICE.
JUST AFTER MIDNIGHT, DEPUTY
WARREN SCOTT HOGAN ACCOMPANIED
HER BACK TO THE HOME ON EDMORE
ROAD IN CHESTERTOWN TO GET HER
BELONGINGS.
>> THE SUSPECT WENT INTO A BACK
ROOM OF THE RESIDENCE AND
OBTAINED A SHOTGUN.
HE CAME OUT OF THE ROOM AND
FIRED ONE ROUND.
HE THEN CONTINUED WALKING TOWARD
THE DEPUTY AND WAS IN CLOSE
PROXIMITY WHEN THE SUSPECT AND
THE DEPUTY EXCHANGED GUNFIRE.
BOTH WERE STRUCK BY THE OTHER'S
GUNFIRE.
KIM: THE SUSPECT, 52-YEAR-OLD
JAMES RICH, DIED AT A NEARBY
HOSPITAL. DEPUTY HOGAN WAS FLOWN
TO SHOCK TRAUMA WITH A SHOTGUN
WOUND TO THE TORSO UNDER HIS
BODY ARMOR.
>> HE WAS AWAKE AND TALKING, BUT
CLEARLY CRITICALLY INJURED.
WE GOT HIM TO THE OPERATING
ROOM.
WE'VE COMPLETED AT LEAST THE
FIRST OF HIS OPERATIVE
PROCEDURES.
HE'S STILL QUITE ILL, BUT WE ARE
HOPEFUL.
>> WE WERE THERE WHEN HE FIRST
WOKE UP OUT OF SURGERY.
HE LOOKS LIKE HE'S IN GOOD
SPIRITS AS BEST HE CAN BE FOR
THE TRAUMATIC EVENT THAT
OCCURRED.
KIM: THE QUEEN ANNES' COUNTY
SHERIFF SAYS DEPUTY HOGAN IS A
4-YEAR VETERAN OF THE FORCE,
AFTER SERVING 7-YEARS WITH
ANOTHER LAW ENFORCEMENT AGENCY.
>> HE'S A REALLY GREAT GUY.
WE'VE BEEN HERE THE ENTIRE TIME
WITH HIM AND HIS FAMILY,
SUPPORTING THEM AND HELPING THEM
GET THROUGH THIS VERY TRAUMATIC
EVENT.
DEBORAH: DEPUTY HOGAN WAS
WEARING A BODY CAMERA, BUT THE
-------------------------------------------
Man arrested in Virginia Beach for allegedly sex trafficking a minor - Duration: 1:36.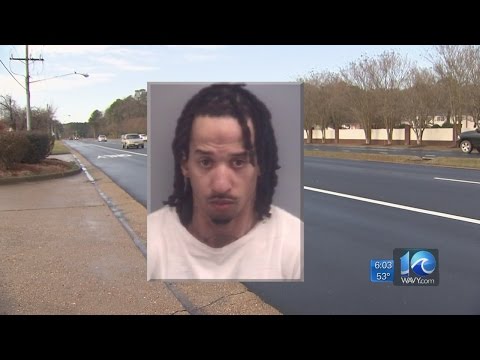
POLICE, THOUGH, HAVE NOT
RELEASED ANY SUSPECT INFORMATION
JUST YET.
VIRGINIA BEACH
POLICE HAVE A
CASE OF SEX TRAFFICKING IN THE
CITY AND THE SUSPECT IS NO
STRANGER TO
POLICE.
POLICE SAY 32-YEAR-OLD ANTHONY
COLEMAN WAS PIMPING OUT A
TEEN
AND FACES SEVERAL CHARGES.
THE CATCH, HE IS ALREADY A
REGISTERED SEX OFFENDER
ELSEWHERE.
10 ON YOUR SIDE'S
JASON MARKS,
YOU'LL SEE ONLY HERE.
JASON: THE PAPERWORK HASN'T
BEEN FILED IN COURT YELLS, BUT
HERE IS WHAT WE WERE
ABLE TO
PIECE TOGETHER.
ON SHORE DRIVE EARLY MORNING
WHERE A 32-YEAR-OLD MAN WAS
USING A CHILD TO SELL SEX.
ANTHONY COLEMAN WAS DRIVING
THE
JUVENILE TO SEX APPOINTMENTS.
HE WAS ALSO CHARGED WITH TAKING
MONEY THE JUVENILE EARNED AND
SEX
TRAFFICKING.
HE IS NOW BEING HELD IN THE
VIRGINIA BEACH JAIL ABOUT 3 1/2
HOURS FROM HIS
HOME IN
WASHINGTON, D.C.
POLICE AREN'T SAYING MUCH ABOUT
THE CASE.
WE DON'T KNOW HOW
HE WAS CAUGHT
OR THE AGE OF THE CHILD HE WAS
WITH.
WHAT WE DO KNOW IS HE
HAS A
HISTORY OF SEX CRIMES.
10 ON YOUR SIDE DUG INTO HIS
PAST AND WE FOUND HE
IS A
CONVICTED RAPIST.
HE WAS FOUND GUILTY OF THE CRIME
BACK
IN 2007 IN MARYLAND.
COURT RECORDS SAY HE SERVED 18
MONTHS BEHIND
BARS.
PRINCE GEORGES COUNTY SAYS HE
WAS ALSO ARRESTED FOR KIDNAPPING
AND RAPE IN
2011, BUT THOSE
CHARGES WERE THROWN OUT WHEN THE
CASE WENT TO COURT.
COLEMAN WILL MAKE
HIS FIRST
COURT APPEARANCE IN VIRGINIA
BEACH FIRST THING TOMORROW
MORNING.
HE DID DECLINE MY REQUEST
FOR
-------------------------------------------
Compare Loom & Leaf-------------------------------------------
Wheels On The Bus Rhyme-------------------------------------------
Mercedes-Benz B-Klasse 160 BLUEEFFICIENCY - Duration: 1:33.-------------------------------------------
Former Superstar Says He's Returning to WWE, Plans for A.J. Styles | Wrestling Report - Duration: 1:51.-------------------------------------------
VW Tiguan - Duration: 1:01.-------------------------------------------
Love Fousey?
-------------------------------------------
For more infomation >> Love Fousey?-------------------------------------------
Disney Style Unboxing
-------------------------------------------
For more infomation >> Disney Style Unboxing-------------------------------------------
Victor Socaciu - Îmbrățișare-n cer - Duration: 3:35.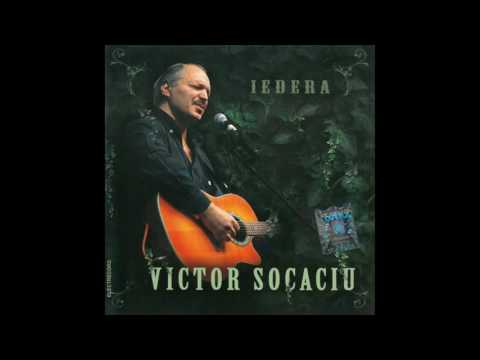
-------------------------------------------
For more infomation >> Victor Socaciu - Îmbrățișare-n cer - Duration: 3:35.-------------------------------------------
Love FouseyTube?
-------------------------------------------
Disney Style Unboxing
-------------------------------------------
President Obama Protects 1.35M Acres With Two New Monuments - Duration: 0:59.
-------------------------------------------
Town of Beaufort's fire department to move into $3.2M upgrade - Duration: 1:49.
FOR FOLKS LIVING IN BEAUFORT...
A NEW FIRE DEPARTMENT BUILDING
IS COMING TO TOWN. THE THREE
POINT TWO MILLION DOLLAR
PROJECT'S BEEN IN THE WORKS FOR
THE LAST 10 YEARS....AND IT'S
ALMOST SET TO OPEN. WNCT'S
ELIZABETH TEW TAKES A LOOK AT
HOW THE NEW BUILDING IS HELPING
THE FIRE DEPARTMENT GROW AND
WHAT IT MEANS FOR RESIDENTS
LIVING IN THE AREA.
"IT'S A BEAUTIFUL STATION."
FROM THIS.....
TO THIS....
THE TOWN OF BEAUFORT'S FIRE
DEPARTMENT IS GETTING A MAJOR
UPGRADE.
"WE ARE READY TO GROW WITH THE
TOWN. IT'S BEEN A LONG TIME
COMING."
THE NEW 12,500 SQUARE FOOT
FACILITY IS TAKING
THE PLACE OF THE DEPARTMENT'S
CURRENT 56-HUNDRED ONE JUST A
FEW BLOCKS
UP THE ROAD.
"THERE WILL BE SIX BEDROOMS AND
3 BATHROOMS...A TRAINING
ROOM...THREE DRIVE THRU
BAYS....A TOOL ROOM....IT'S
GONNA BE A HEAD TURNER."
THE CHIEF SAYS THE CURRENT
BUILDING IS
TOO SMALL FOR ITS GROWING
DEPARTMENT. "WE'RE ELBOW TO
ELBOW. WE'VE GOT ROOMS...WELL MY
DESK IS IN THE LOBBY."
IT WILL ALSO BE AN IMPROVEMENT
TO THE
TOWN'S FIRE RATINGS.
THE NEW BUILDING HAS THREE BAYS
WHICH WILL HOLD UP TO SIX
TRUCKS. THE CURRENT ONE HAS
FOUR.
ADDING THE ADDITIONAL TRUCKS
HAS FOUR.
ADDING THE ADDITIONAL TRUCKS
WILL CUT DOWN ON INSURANCE
PREMIUMS. "LIKE A KID AT
CHRISTMAS."
FIRE CHIEF "LARRY FULP'S" BEEN
WITH THE
DEPARTMENT FOR NEARLY 40 YEARS.
"WE'VE BEEN TRYING TO GET THIS
FOR QUITE A WHILE. IT WILL
GIVE US MORE ROOM TO MOVE AROUND
IN...MORE ROOM FOR
BUSINESS...AND A LOT MORE ROOM
FOR TRAINING."
HE SAYS THE DESIGN IS MEANT TO
REFLECT THE CURRENT FEEL OF
BEAUFORT...WITH DARK
BRICK...LARGE GLASS WINDOWS AND
AN ASYMETRICAL STYLE.
THAT'S SOMETHING RESIDENTS SAY
THEY CAN GET BEHIND.
"IT'S GOING TO BE A GREAT
ADDITION TO THE TOWN. I'M
EXCITED TO SEE IT OPEN AND
RUNNING." IN BEAUFORT ELIZABTH
TEW NINE ON YOUR SIDE.
THE OLD BUILDING WILL BE PUT UP
FOR
SALE.
THE FIRE DEPARTMENT IS FINISHING
UP PACKING AND GETTING READY FOR
THE MOVE.
IT HOPES TO BE IN THE NEW
BUILDING BY FEBRUARY.
-------------------------------------------
BMW 5 Serie 528I -M-SPORT -HIGH EXECUTIVE ,Panodak, Sportleer, - Duration: 1:44.
-------------------------------------------
UK to face-off with Georgia Tech in Taxslayer Bowl - Duration: 1:48.
.
DAN KOOB HAS MORE FROM
JACKSONVILLE, FLORIDA.
DAN: UK HOPES ITS BOWL CHANCES
ARE BETTER THAN JOJO KEMP'S ODDS
AT HITTING A GOLF BALL.
THE CATS TOOK A SWING AT TOP
GOLF A STONE'S THROW AWAY FROM
THE UNIVERSITY OF NORTH FLORIDA
WHERE THEY HELD A WALKTHROUGH
THIS AFTERNOON WHICH IS CLOSE BY
TO EVER BANK FIELD.
JUST BEHIND ME, THE SITE OF THE
2016 TAX SLAYER BOWL.
KENTUCKY HASN'T PLAYED IN OVER A
MONTH.
IT'S GIVEN THE COACHING STAFF
PLENTY OF OPPORTUNITY TO STUDY
AN UNORTHSDOXED GEORGIA TECH
OFFENSIVE ATTACK.
IT'S AN OFFENSE THAT IS
AVERAGING THE 10TH MOST RUSHING
YARDS PER GAE IN THE COUNTRY.
>> WE'VE REALLY, YOU KNOW,
HASHED IT OUT FOR A LONG TIME.
WE'VE SPENT SOME TIME -- A LOT
OF TIME ON THESE GUYS AS YOU
KNOW.
>> IF YOU JUST DO LIKE YOU TO
YOUR JOB AND READ WHAT YOU'RE
SUPPOSED TO DO, IT'S NOT THAT
BAD.
>> IT'S PRETTY HARD TO YOU KNOW,
TO LOOK ON FILM AND SAY, OK, I'M
SURPRISED THAT, YOU KNOW, A
COLLEGE FOOTBALL TEAM SORT OF
RUNS THIS BUT, YOU KNOW, AT THE
END OF THE DAY, UM, IT'S
EFFECTIVE.
I MEAN, LOOK AT THE POINTS THOSE
GUYS PUT UP IN THE TRIPLE-OPTION
TEAM LIKE THAT.
IT'S DESIGNED TO EAT THE CLOCK.
IF YOUR EYES ARE IN THE RIGHT
SPOT AND YOU PLAY YOUR DEPTH,
YOU'LL BE SOUND.
DAN: THE CATS ALLOWED 225 YARDS
PER GAME TO OPPOSING RUSHERS.
HEAD COACH MARK STOOPS WANTS HIS
SECONDARY ON HIGH ALERT, TOO.
>> THEY HAVE TO BE GREAT OFF
THEIR -- ON THEIR ROTATIONS AND
WHAT WE'RE DOING AND PLAYING
PLAY ACTION.
REPORTER: DESPITE NOT BEING IN A
BOWL GAME SINCE 2010, EVERYONE
AROUND THIS TEAM SEEMS TO BE
EXTREMELY CONFIDENT.
PLAYERS AND COACHES A-LIKE.
I ASKED RUNNING BACK BOOM
WILLIAMS WHAT HE ATTRIBUTES THE
LASER-LIKE FOCUS AND ATTENTION
TO.
HE SAID IT'S VERY SIMPLE, THEY
WANT TO SEND THESE SENIORS OUT
-------------------------------------------
Website Obtains Trump's Driver's License, Finds Discrepancy - Duration: 3:10.
Website Obtains Trump�s Driver�s License, Finds Discrepancy.
by Krystle Vermes.
A copy of President-elect Donald Trump�s New York driver�s license was obtained by
Politico, which published it Friday.
The website noted the license lists him as 6-foot-2, contradicting statements by Trump
and his doctor that he is 6-foot-3.
�The Trump transition did not respond to a request for comment about the height listed
on his driver�s license,� Politico reported.
The website said it obtained Trump�s license �through an open-records request related
to the central Virginia winery that�s owned by Trump and run by his son Eric.�
Politico noted that a Time magazine profile this year said Trump is 6-foot-3 and �it
irritates him that so many media outlets say 6-foot-2.�
In September, Trump appeared on The Dr. Oz Show, featuring Dr. Mehmet Oz, a cardiothoracic
surgeon.
On the program, Trump presented a letter from his gastroenterologist that stated he was
6-foot-3.
�He has had an annual physical exam in the spring of every year,� specified Dr. Harold
Bernstein.
The letter went on to state more health data, including Trump�s cholesterol levels, weight
(236 pounds), blood pressure and blood sugar levels.
�The study was reported within range of normal,� the doctor concluded.
�There is no family history of premature cardiac or neoplastic disease.�
In terms of medications, Bernstein noted that Trump takes a lipid lowering agent (rosuvastatin)
and a low-dose aspirin.
Shortly after the information was released and the television show aired, the liberal
website Slate published an article about the Trump height discrepancy and his body mass
index.
BMI is the weight-to-height ratio medical professionals use to categorize individuals
as �underweight, �normal weight� or �overweight.�
�Is it possible that Trump�s doctor added the extra inch so that his patient, who is
not exactly lacking in vanity, would not be �officially� obese?� wrote Slate author
Susan Matthews.
�Is it irresponsible to speculate?
It is irresponsible not to.�
However, Slate acknowledged that �BMI is a worthless measure of physical health.�
In October, The Washington Post attempted to determine Trump�s height by comparing
photos of the president-elect next to others.
While there was not a definitive answer, the publication noted that if Trump were under
6-foot-3 and 236 pounds, he would be �obese,� according to his BMI.
What do you think?
Scroll down to comment below.
-------------------------------------------
Denton police officer helps mother in need - Duration: 1:58.
-------------------------------------------
LuHan - Let Me Stay By Your Side { See You Tomarrow OST }( ADAPTACION PARA COVER ESPAÑOL ) - Duration: 2:29.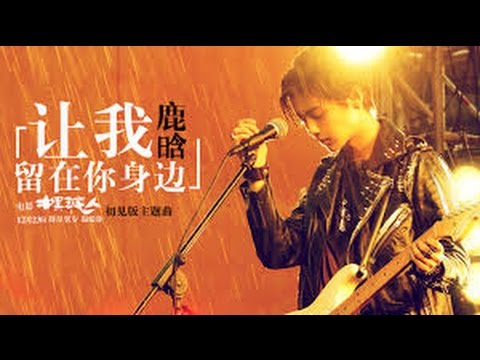
-------------------------------------------
Bulgogi with Bean Sprouts (불고기 + 콩나물 = 콩불) - Eating Korean Food in Seoul, Korea - Duration: 8:17.
Alright, so time for another delicious lunch in Seoul (서울).
Yeah, exactly.
So today we're going for a very classic Korean dish.
We're having Bulgogi (불고기) which literally means 'fire meat' and we've placed our order.
We've also ordered something else that is a bit of mystery and we'll show it to you
when it arrives.
So there is a lot happening at the table right now.
Our two orders have arrived.
And the first one is cooking.
We also have our little side dishes and some soup.
So if you have a look here we have Miyeok guk (미역국) which is a seaweed soup.
And they've given us a little bowl so we can just serve ourselves.
Yeah, this is one of our favorite little side soups that are often served at Korean restaurants.
And it is so healthy.
You can feel good about eating this.
it is really what is interesting to is that if I remember correctly you're supposed to
eat this on your birthday.
It is special birthday food.
Oh yeah.
To live a long life.
Maybe?
Here is yours.
So why don't you try it.
Okay, I'm going to serve myself now.
Okay.
I was a kind wifey.
My first one.
So yeah, you can see the big thick pieces of seaweed in there.
Seaweed.
Unlike some of the other seaweed products you get in Korea the seaweed here isn't salty.
It is just cooked as it is.
How is that?
It is really nice.
It is like even lighter than a miso soup.
It is super light.
Really tasty.
I like it.
Alright, so the first dish here has finished cooking.
So you can see it sizzling.
Here is the classic Bulgogi (불고기) and this is one of my favorite Korean foods.
It is just amazing and I haven't had this in a long time.
This is my first time to have it since we came back to Seoul (서울).
So if we take a look down here we'll show you some of the ingredients.
So here you can see the strips of meat and they've what really makes Pulgogi (불고기)
so delicious is that the marinade.
The marinade is just awesome.
A sweet marinade.
It is a very sweet marinade.
So it is made with soy sauce, sugar, sesame seed sauce and it also has garlic and peppers.
Pepper in it too.
It is just an amazing sauce.
That is really what makes it.
And you can also see here we have a what I think it called Kongnamnul (콩나물) which
are the bean sprouts.
The beansprouts.
Yeah.
And we also have some tteok (떡).
Some rice cakes.
Korean rice cakes.
So we've got a lot of different things going on.
And some noodles.
I saw some glass noodles in there earlier.
Right, there is also some glass noodles here.
Alright.
See if we can find them.
Right there.
There you go.
So you have a lot going on.
Alright, let's dish it up.
Okay.
There we go.
So I'm going to put in a little bit like this.
And then I'm going to grab some of the sauce because that is the best part.
Haha.
Can't leave that behind.
Yeah, I'm going to drown and put that sauce in.
Okay, it is looks like it is piping hot.
Straight from the pan so you know what I'm going to eat this properly with chopsticks.
There we go.
Going in for the first bite.
Going to blow on that a bit.
Don't burn yourself in the process.
Oh, how is that?
Wow!
That is the real deal.
Yeah.
That is classic Bulgogi (불고기) and it the sauce that makes it taste so good.
Mmmm.
Yeah.
Those thin slices of meat.
This restaurant specializes in Bulgogi (불고기) so they have so many different variations
and I'm really excited to try the next one.
Yeah.
Alright, so the second one that we ordered is ready.
Sam, you know the name.
What is this one called.
Yeah.
It is called Cheese Kongbul (치즈 콩불).
Alright so it is a cheese Kongbul (치즈 콩불) and we have never had this before.
This is Korean food we have yet to try.
It was amazing.
The guy came and cooked both dishes for us.
Yeah.
And then once this one was done he added cheese and all over it and it has just been melting
and getting sticky and gooey.
It kind of looks like something in between Bulgogi (불고기) and tteokbokki (떡볶이)
with cheese.
Haha.
Yeah.
Let's try it.
It has got a lot going on.
So what can we can tell from the ingredients that we have so far?
Alright, well again we have your beansprouts.
We have some onions, we have rice cakes, the beef of course the bulgogi (불고기).
Lots of cheese.
Um, and yeah I think it is going to be spicy.
I'm seeing some of the red pepper happening here.
Okay, let's try it.
You can see the cheese.
Oh my god.
Is it good?
That is really good.
Haha.
Yeah, it was one on the menu it had a little star beside it saying this is a hit.
You know one of the best things.
It is super spicy.
Oh my.
Super spicy.
My eyes are actually watering right now.
Do you think they use a gochujang sauce (고추장) possibly?
Red pepper paste.
Definitely.
And it is so cheesy and gooey.
I feel like I'm having Korean pizza toppings in a way.
This is amazing.
Wow.
See.
To all our viewers it is worth trying new things.
We have never had this before.
First time reaction.
This is incredible.
I haven't even tried the other one yet but I already know this is going to be my favorite.
Even if it is making me tear up.
Like this one is really fire-y.
I know Bulgogi (불고기) meat is fire meat because you cook it over the fire but this
is like burning my whole throat.
Sam is going for the cheese and the spice.
Yeah, so I loaded up a little portion here.
So let's see how that is.
You're going to feel it.
Oh wow.
In a matter of seconds.
Yeah.
That is really spicy as you said.
Loved the addition of cheese.
Of course you did.
It is not like a traditional Korean ingredient but whenever you add cheese to something like
this it really does enhance it.
I like it.
I probably like the Bulgogi (불고기) a little bit more.
Really?
Yeah.
But I do like this though.
Alright, so I'm going to try more of the classic recipe right now.
The Pulgogi (불고기).
The sweet one.
My mouth is like still watering from all that spice.
I'm like salivating over here.
That second one that we ordered really was spicy.
Yeah.
We still have more to eat of it too.
Okay, going in for my first bite.
Let's get some noodles, some beef, some beansprouts.
Look at that.
It is still steaming.
Mmmm.
I'm eating my own hair.
How gross.
Mmmm.
How do you like that?
One second.
Hang on I'm choking.
Okay, so this one is definitely a lot milder.
Really sweet but after having the spicy one with cheese I don't know if I liked burned
my taste buds or what or numbed them but this one isn't as flavorful in comparison so I'm
going to have to go for the spicy one.
Spice and cheese.
That was a hit in my books.
And it is a hit on the menu so that is how you know it is good.
So I think it is fair to say that our only complaint is that the portions could be a
lot bigger.
Because we just polished that off in seconds and it was so good that now we're scrapping
the plate.
Yeah, we took care of that.
Nothing left.
We took care of that.
Although in terms of the price point they were eight thousand Won (원) each.
So sixteen thousand Won (원) in total.
Which is ₩16,000 KRW.
So you're looking at about thirteen or forteen US dollars for those dishes.
And yeah they were really tasty.
Yeah, and that also came of course with the banchan (반찬), the sides, the rice which
we kind of ignored because the beef was so tasty.
Yeah and the Miyeok guk (미역국) soup.
So yeah, there was a lot of food but we really keyed in on the principle courses.
Không có nhận xét nào:
Đăng nhận xét